Leading Film Faced Plywood Manufacturing
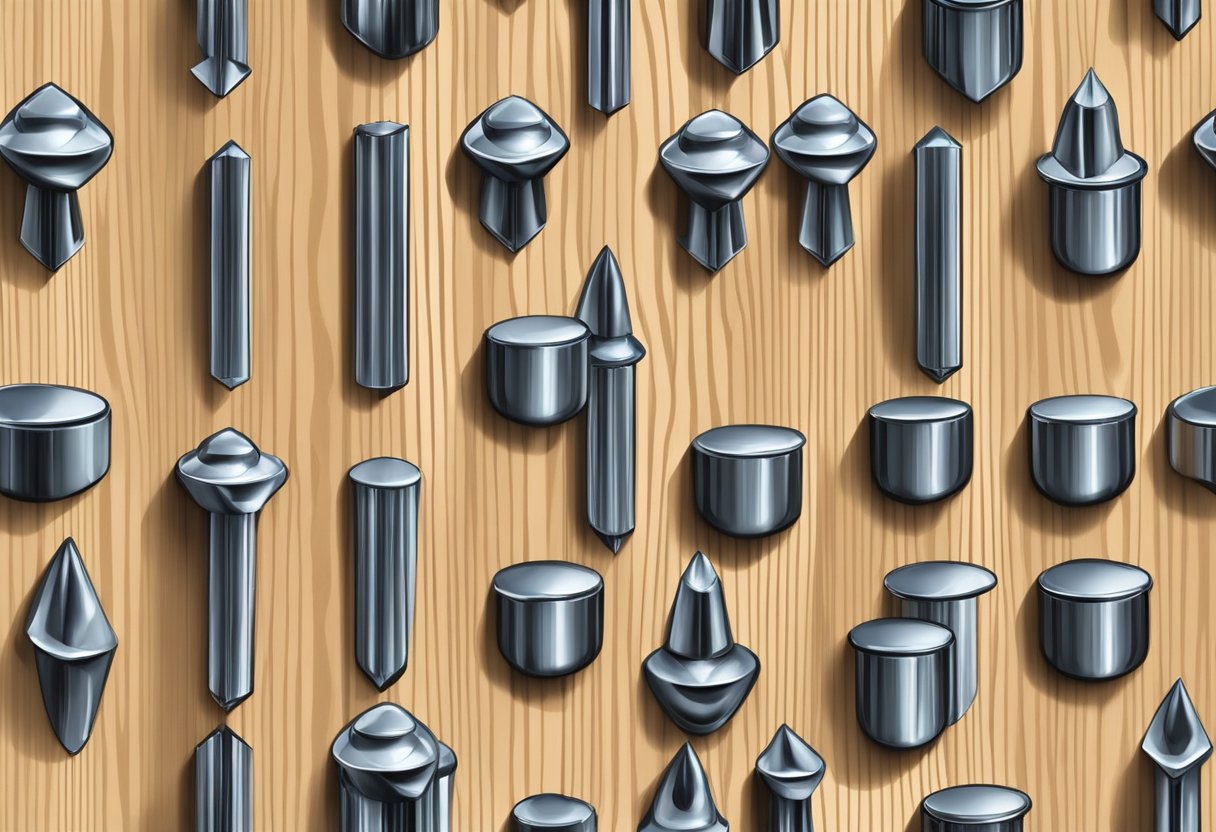
Leading Film Faced Plywood Manufacturing
Laminated Veneer Lumber (LVL) studs are an engineered wood product that has been gaining popularity in recent years. LVL studs are made by layering thin sheets of wood veneer together with glue to create a strong and stable material that is ideal for framing. LVL studs are stronger and more uniform than traditional lumber, making them a great choice for a wide range of applications.
One of the main advantages of LVL studs is their strength. LVL studs are stronger than traditional lumber, which means they can support heavier loads and span longer distances without sagging or warping. This makes them ideal for use in tall walls, long spans, and other applications where strength is critical. Additionally, LVL studs are more uniform in size and shape than traditional lumber, which makes them easier to work with and results in less waste.
LVL studs are also an environmentally friendly choice. Because they are made from fast-growing trees and use less wood than traditional lumber, they are a more sustainable choice. Additionally, the manufacturing process for LVL studs produces less waste and uses less energy than the process for producing traditional lumber. As a result, LVL studs are an excellent choice for those who are concerned about the environment.
Laminated Veneer Lumber (LVL) is an engineered wood product that has gained popularity in recent years as a viable alternative to traditional lumber for wall framing. LVL studs are made by bonding thin wood veneers together with adhesives under heat and pressure to create a strong and durable product. In this section, we will provide an overview of LVL technology, its history, and the properties of LVL studs.
LVL technology was first developed in the 1970s in New Zealand and quickly spread to other countries. The technology was initially used in the construction of large beams and columns in commercial and industrial buildings. However, with the increasing demand for sustainable and cost-effective building materials, LVL technology has now been adapted for use in wall framing.
LVL studs offer several advantages over traditional lumber studs. They are stronger, stiffer, and straighter, making them ideal for use in wall framing. According to Boise Cascade EWP, LVL studs offer at least 2.1 times more bending strength and 20% more stiffness than No. 2 SPF dimension lumber. They also have eased edges that help prevent splinters.
Moreover, LVL studs are less prone to warping, twisting, or shrinking compared to traditional lumber studs. This means that they provide a more stable and durable framing system, which can lead to better energy efficiency and reduced maintenance costs over time.
In addition, LVL studs are available in longer lengths than traditional lumber studs, which can reduce the number of joints needed in a wall, leading to faster installation times and lower labor costs.
Overall, LVL studs are a reliable and cost-effective alternative to traditional lumber studs that offer superior strength, durability, and stability.
Laminated Veneer Lumber (LVL) is a composite wood product made from thin layers of wood veneer. The raw materials used to manufacture LVL include small diameter logs, wood residues, and other wood by-products. These raw materials are sourced from sustainably managed forests and sawmills.
The production of LVL involves several stages. First, the logs are debarked and cut into small pieces. These pieces are then dried and sorted based on their size and quality. The veneers are then peeled from the logs and sorted again based on their thickness and quality.
Next, the veneers are glued together using a high-pressure process. The glue used is typically a phenol-formaldehyde resin, which is known for its strength and durability. The veneers are arranged in a specific pattern to ensure that the finished product has consistent strength and stiffness.
After the veneers are glued together, the LVL is cut to the desired length and thickness. The finished product is then sanded and graded based on its appearance and strength properties.
Quality control is an essential part of the LVL manufacturing process. During production, the product is tested for strength, stiffness, and other properties to ensure that it meets the required standards. The product is also inspected visually to ensure that it has a consistent appearance and is free from defects.
In addition to these tests, LVL manufacturers also conduct regular audits of their production facilities to ensure that they are operating efficiently and safely. This includes monitoring the use of raw materials, the performance of the equipment, and the quality of the finished product.
Overall, the manufacturing process for LVL is a complex and precise process that requires careful attention to detail and quality control. The result is a product that is strong, durable, and versatile, making it an excellent choice for a wide range of construction applications.
Laminated veneer lumber (LVL) studs are versatile and can be used in a variety of applications. Here are some common uses for LVL studs:
LVL studs are commonly used in residential construction. They are ideal for load-bearing walls and can be used in place of traditional lumber studs. LVL studs are straighter and more uniform in size than traditional lumber, which can make installation easier and faster. They are also less prone to warping, twisting, and splitting, which can result in a more stable and durable structure.
In addition to load-bearing walls, LVL studs can be used for headers, beams, rafters, and joists. They can also be used as columns and I-joist flange material. Two or three sections of SCL can be joined together to form 3-1/2-inch or 5-1/4-inch members. These thicker sections readily nest into 2×4 or 2×6 framed walls as headers or columns.
LVL studs are also used in commercial projects. They are ideal for applications where strength and durability are critical. LVL studs can be used for load-bearing walls, as well as for headers, beams, and columns. They are also commonly used in the construction of tall buildings, where their strength and stiffness make them an excellent choice for resisting wind loads.
In addition to their strength and durability, LVL studs are also environmentally friendly. They are made from fast-growing, renewable wood species, which means they are a sustainable choice for construction projects.
Overall, LVL studs are a versatile and reliable choice for a variety of construction applications. Whether you are building a residential home or a commercial building, LVL studs can provide the strength, stability, and durability you need.
When handling LVL studs, it is important to keep them dry and protected from the elements. Store them in a dry and covered area, and avoid exposing them to moisture. If the LVL studs become wet, allow them to dry completely before installation to prevent warping or twisting.
When moving LVL stud, lift them from the bottom and avoid dragging them across rough surfaces. If you need to cut or drill the LVL stud, make sure to wear protective gear such as goggles and a dust mask.
Before installation, make sure to check the manufacturer’s instructions for specific guidelines. Here are some general best practices to follow:
By following these guidelines, you can ensure that your LVL stud are installed properly and will provide reliable structural support.
LVL stud have been gaining popularity in the construction industry due to their durability, strength, and cost-effectiveness. The market for LVL stud is expected to grow steadily in the coming years, driven by several factors.
One of the key drivers of the LVL stud market is the increasing demand for sustainable and eco-friendly building materials. LVL stud are made from renewable resources and have a lower carbon footprint compared to traditional building materials. This makes them an attractive option for builders and developers who are looking to reduce their environmental impact.
Another factor driving the growth of the LVL stud market is the increasing demand for affordable housing. LVL stud are an excellent alternative to traditional building materials such as concrete and steel, which can be expensive and time-consuming to install. LVL stud are lightweight, easy to install, and require minimal maintenance, making them an ideal choice for affordable housing projects.
In addition to these factors, the LVL stud market is also being driven by advancements in technology. Manufacturers are investing in research and development to create new and innovative products that are stronger, more durable, and more cost-effective than ever before. This has led to the development of LVL stud that are capable of withstanding extreme weather conditions, earthquakes, and other natural disasters.
Overall, the future outlook for the LVL stud market is bright. With increasing demand for sustainable and eco-friendly building materials, affordable housing, and advancements in technology, the LVL stud market is poised for steady growth in the coming years.
If you are interested in any of our products or would like to discuss a customized order, Please feel free to contact us.