Leading Film Faced Plywood Manufacturing
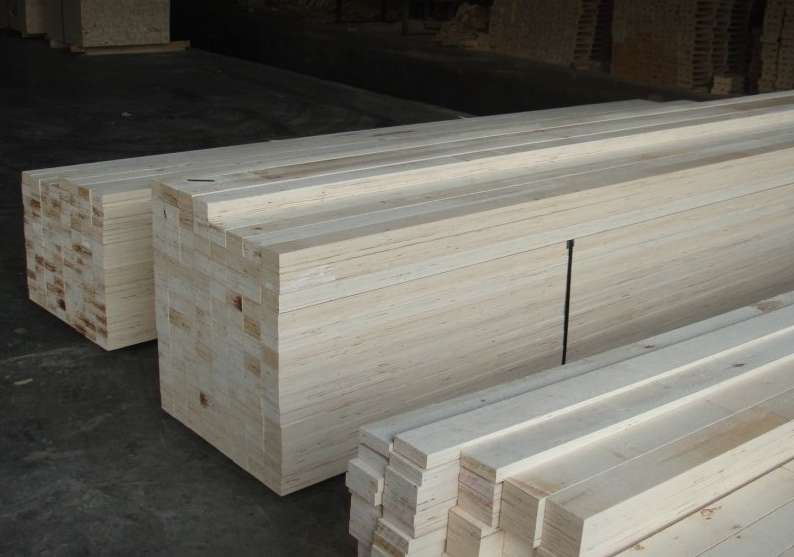
Leading Film Faced Plywood Manufacturing
If you’re in the construction industry or simply interested in different types of wood products, you may have heard the terms LVL and LVB. These two types of engineered wood products are becoming increasingly popular due to their strength, versatility, and durability. In this article, we’ll explore the differences between LVL and LVB and their common applications.
Laminated Veneer Lumber (LVL) is an engineered wood product made by layering thin wood veneers together with adhesives. The layers are oriented in the same direction, which gives LVL its high strength and stability. LVL is an excellent substitute for traditional lumber, as it can be made in larger sizes and has a more uniform quality. It is commonly used for structural applications such as beams, headers, and rim boards. LVL is also used for door frames, scaffolding panels, and packaging timbers, among other things.
Laminated Veneer Board (LVB) is another type of engineered wood product that is made by assembling plywood veneers in a specific orientation. LVB has a different structure and performance than LVL and is used for different applications. LVB is commonly used for core structures within wood-based panels that are not specifically LVL or normal plywood. The arrangement of the veneers in LVB can vary, which affects its strength and stability. LVB is used for furniture, flooring, and wall panels, among other things.
LVL and LVB are both types of engineered wood products made by layering veneers in a specific orientation and bonding them with adhesives. LVL stands for laminated veneer lumber, while LVB stands for laminated veneer board. Both products are known for their superior strength, stability, and consistency compared to traditional solid wood products.
LVL is made by arranging veneers in the same direction and bonding them together with adhesives. This creates a product that is stronger and more stable than solid wood of the same size. LVL is often used in construction for beams, headers, and other load-bearing applications.
LVB, on the other hand, is made by layering veneers in a specific pattern. While the veneers are not all arranged in the same direction like LVL, they are still bonded together with adhesives to create a strong and stable product. LVB is often used for furniture, cabinetry, and other decorative applications.
Both LVL and LVB offer many advantages over traditional solid wood products. They are more consistent in strength and size, have better resistance to warping and splitting, and are more environmentally friendly since they use less wood than solid wood products.
Laminated Veneer Lumber (LVL) and Laminated Veneer Board (LVB) are engineered wood products manufactured from multiple thin layers of veneer that are aligned with the length of the finished lumber. LVL and LVB are made from different species of wood, including pine, spruce, and fir, which are sourced from local and sustainably managed forests. The veneers are then sorted and graded based on their thickness, strength, and other properties.
The manufacturing process of LVL and LVB involves several steps. First, the veneers are dried and sorted to remove any defects. Then, they are glued together with a waterproof adhesive to form a large panel. The panel is then cut to the desired size and shape using a saw. Finally, the edges are sanded to create a smooth finish.
One of the key advantages of LVL and LVB is their strength and durability. They are stronger and more stable than traditional lumber, making them ideal for structural applications such as beams, headers, and rim boards. They are also more uniform in size and shape, which makes them easier to work with and reduces waste.
In conclusion, the manufacturing process of LVL and LVB involves sourcing high-quality wood from sustainable forests and using advanced production techniques to create a strong and durable engineered wood product.
Laminated Veneer Lumber (LVL) and Laminated Veneer Board (LVB) are versatile engineered wood products that have a wide range of applications in the construction and furniture design industries.
LVL and LVB are ideal for structural applications that require high strength and durability. They are commonly used as headers, beams, and rim boards in residential and commercial construction. Due to their superior strength, they can span longer distances than traditional wood products, reducing the need for intermediate supports. Additionally, they are more uniform in size and strength than solid wood, making them easier to work with and reducing waste.
LVL and LVB are also used in the manufacturing of prefabricated building components such as trusses, columns, and panels. These components can be produced off-site and then quickly assembled on-site, reducing construction time and labor costs.
LVL and LVB are increasingly being used in furniture design due to their strength, stability, and aesthetic appeal. They can be used to create unique and modern designs while also providing the necessary support for furniture pieces. LVL is commonly used for table legs, chair frames, and shelving due to its ability to withstand heavy loads. LVB is often used for decorative panels and surfaces due to its smooth finish and uniform grain pattern.
In addition, LVL and LVB can be used to create curved and shaped furniture pieces that would be difficult or impossible to achieve with traditional wood products. This is due to their ability to be molded and shaped while still maintaining their strength and durability.
Overall, the versatility and strength of LVL and LVB make them ideal for a wide range of applications in the construction and furniture design industries.
Laminated Veneer Lumber (LVL) and Laminated Veneer Board (LVB) are engineered wood products that have gained popularity in the construction industry due to their strength and durability. Unlike traditional lumber, LVL and LVB are made by bonding multiple thin layers of wood veneers together using adhesives, resulting in a stronger and more stable product.
Compared to other engineered wood products like Plywood and Oriented Strand Board (OSB), LVL and LVB have higher strength and stiffness, making them ideal for applications where high load-bearing capacity is required. LVL and LVB are also less prone to warping, twisting, and splitting, which makes them more durable and long-lasting.
In addition to their strength and durability, LVL and LVB are also considered sustainable building materials. Both materials are made from fast-growing trees that are harvested from sustainably managed forests. This makes them a more environmentally friendly option compared to traditional lumber, which is often sourced from old-growth forests.
Moreover, the manufacturing process of LVL and LVB involves using less wood than traditional lumber, which reduces the impact on the environment. The adhesives used in the production of LVL and LVB are also low-VOC (volatile organic compound) and formaldehyde-free, which means they are less harmful to the environment and human health.
Overall, LVL and LVB are strong, durable, and sustainable building materials that offer several advantages over traditional lumber and other engineered wood products. Whether you’re building a new home or renovating an existing one, LVL and LVB are worth considering for their superior strength, durability, and sustainability.
When handling LVL and LVB beams, it’s important to take certain precautions to prevent damage. The beams should be stored in a dry, covered area to prevent moisture damage. When storing the beams, they should be stacked flat and not on their edges to prevent warping. If the beams need to be moved, they should be lifted by the ends and not the middle to prevent sagging. When cutting the beams, make sure to use a sharp blade to prevent splintering and tear-out.
Proper long-term care of LVL and LVB beams can help extend their lifespan. It’s important to keep the beams dry and free of moisture to prevent rot and decay. Inspect the beams regularly for signs of damage such as cracks or splitting. If any damage is found, it should be repaired immediately to prevent further damage. To clean the beams, use a soft-bristled brush or cloth to remove any dirt or debris. Avoid using harsh chemicals or solvents as they can damage the beams.
Overall, LVL and LVB beams are durable and long-lasting when installed and maintained properly. By following these guidelines, you can ensure that your beams will provide reliable support for years to come.
Q: What does “LVL LVB” stand for? A: “LVL LVB” typically stands for “Level Love” or “Love Level,” depending on the context. It often refers to a concept related to leveling up or progressing in love or relationships.
Q: Is “LVL LVB” a specific term in a certain field or community? A: While it’s not a widely recognized acronym or term in any particular field, it’s sometimes used in social media, gaming, or online communities to express the idea of advancing or deepening romantic feelings or relationships.
Q: How is “LVL LVB” used in everyday language? A: People might use “LVL LVB” as a hashtag or shorthand on social media platforms to caption posts about romantic milestones, such as anniversaries, declarations of love, or significant moments in relationships.
Q: Can “LVL LVB” have other meanings or interpretations? A: Since language is flexible and can be interpreted subjectively, “LVL LVB” might be understood differently depending on the context or personal perspective. However, its most common interpretation is related to romantic affection or relationship progression.
Q: Is “LVL LVB” part of a larger concept or trend? A: It could be seen as part of a broader trend of using gaming or internet culture references to express emotions or experiences in non-gaming contexts. It reflects how digital language and symbols influence communication across various platforms.
Q: Are there any variations of “LVL LVB” that I should know about? A: While “LVL LVB” is the most common form, variations like “LVL UP LOVE” or “LVB UP” might also be used to convey similar sentiments of growth or advancement in love.
If you are interested in any of our products or would like to discuss a customized order, Please feel free to contact us.