Leading Film Faced Plywood Manufacturing
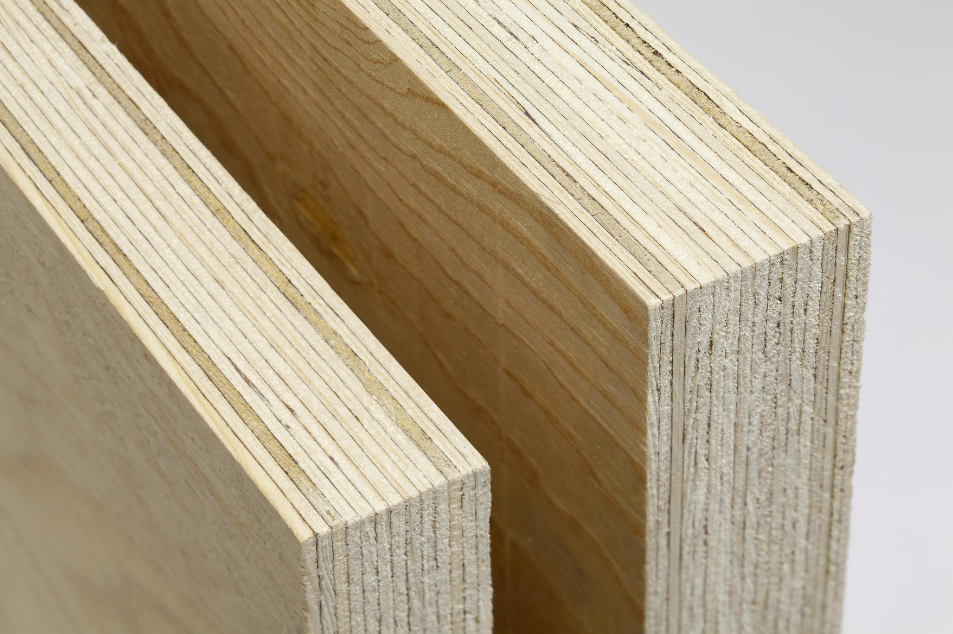
Leading Film Faced Plywood Manufacturing
If you’re planning on building or renovating a house, you should know about LVL lintels. LVL stands for Laminated Veneer Lumber, which is an engineered wood product made from thin layers of wood veneer. LVL lintels are used to support the weight of the structure above openings such as windows and doors.
Compared to traditional timber lintels, LVL lintels have several advantages. They are stronger, more durable, and less prone to warping or twisting. They also have a higher load-bearing capacity, which means that they can support heavier loads without the need for additional support. Additionally, LVL lintels are more resistant to moisture and insect damage, making them a better long-term investment.
If you’re looking for a reliable and cost-effective solution for your lintel needs, LVL lintels are definitely worth considering. They are easy to install and can be custom-made to fit your specific requirements. Whether you’re building a new house or renovating an existing one, LVL lintels can provide the structural support you need to ensure the safety and stability of your home.
Laminated Veneer Lumber (LVL) is a type of engineered wood made from thin layers of wood veneers glued together. The veneers are usually oriented in the same direction to provide strength and stability. LVL is a popular material for lintels because of its high strength and durability. It is also resistant to warping, twisting, and shrinking, which makes it an ideal choice for long-span lintels.
The design of LVL lintels is based on the principles of structural engineering. The lintel must be designed to support the weight of the masonry above the opening as well as any additional loads such as wind, snow, and seismic forces. The size and shape of the lintel depend on the span of the opening and the loads it must support.
LVL lintels are designed to be installed horizontally above the opening in the masonry wall. The ends of the lintel must be supported by the masonry on either side of the opening. The lintel must be securely fastened to the masonry using appropriate connectors such as bolts or screws.
In conclusion, LVL lintels are a popular choice for long-span openings in masonry walls due to their high strength, durability, and resistance to warping and twisting. When designing and installing LVL lintels, it is important to follow the principles of structural engineering and use appropriate connectors to ensure a secure and safe installation.
When it comes to manufacturing LVL lintels, there are a few key steps involved in the process. These include milling, adhesive application, pressing, and curing. Here’s a closer look at each of these steps:
The first step in the LVL lintel manufacturing process is milling. This involves taking pieces of wood and cutting them into thin veneers. These veneers are typically around 3mm thick and are cut to the desired length and width. The veneers are then sorted based on their strength and appearance.
Once the veneers have been milled, the next step is to apply adhesive to them. Phenol formaldehyde adhesive is commonly used in LVL lintel manufacturing, as it is highly resistant to both weather and boiling. The adhesive is applied to the veneers using a roller or spray system.
After the adhesive has been applied, the veneers are stacked together and pressed under high pressure. This helps to ensure that the adhesive bonds the veneers together firmly. The pressure used during this process can range from 10 to 25 N/mm².
Once the veneers have been pressed together, they are cured in a high-temperature oven. This helps to further strengthen the bond between the veneers and the adhesive. The curing process can take several hours, depending on the thickness of the LVL lintel.
Overall, the manufacturing process for LVL lintels is complex and involves several key steps. However, by following these steps carefully, manufacturers can produce high-quality LVL lintels that are strong, durable, and resistant to a wide range of environmental factors.
Laminated Veneer Lumber (LVL) lintels are engineered wood products that have excellent structural properties. They are made by bonding together thin veneers of wood with adhesives under heat and pressure. LVL lintels are commonly used for load-bearing applications in residential and commercial construction.
LVL lintels have high load-bearing capabilities and can support significant loads over long spans. The load-bearing capacity of an LVL lintel depends on its size, span, and the type of load it is supporting. LVL lintels are available in a range of sizes and can be custom-made to suit specific requirements.
To determine the load-bearing capacity of an LVL lintel, it is important to consider the design loads, including dead loads, live loads, and wind loads. Dead loads are the weight of the lintel itself, while live loads are the weight of the people, furniture, and other objects that the lintel supports. Wind loads are the forces exerted by wind on the building.
Deflection is the amount of bending that occurs in an LVL lintel when it is loaded. Deflection is an important consideration in the design of LVL lintels because excessive deflection can cause cracking in finishes, damage to walls, and other structural problems.
The deflection criteria for LVL lintels are specified in building codes and standards. The deflection limits depend on the span, load, and the type of building. It is important to ensure that the LVL lintel is designed to meet the deflection criteria specified in the building code.
In conclusion, LVL lintels have excellent load-bearing capabilities and meet the deflection criteria specified in building codes. They are a reliable and cost-effective option for load-bearing applications in residential and commercial construction.
When installing LVL lintels, it is essential to follow the manufacturer’s guidelines to ensure proper installation and maximum performance. This section will provide you with a brief overview of the installation guidelines for LVL lintels.
Before installation, it is crucial to handle and store LVL lintels correctly. LVL lintels should be kept dry and protected from the elements. If stored outside, they should be covered with a waterproof cover that allows for ventilation. They should also be stored off the ground and supported evenly to prevent warping.
When handling LVL lintels, it is essential to wear gloves and eye protection to avoid splinters and dust. LVL lintels should always be lifted and carried in a horizontal position to prevent damage or warping.
When placing and fixing LVL lintels, it is crucial to ensure that they are level and straight. The LVL lintel should be bedded on a full bed of mortar and supported by at least 150mm on either end. The masonry above the lintel should be built in accordance with BS EN 1996-2:2006.
It is essential to ensure that the lintel is not overloaded during installation. If necessary, additional temporary supports should be used during the installation process. The temporary supports should be removed once the masonry has cured.
In conclusion, LVL lintels are an excellent choice for structural support in construction projects. By following the manufacturer’s guidelines for handling, storage, placement, and fixing, you can ensure that your LVL lintels provide maximum performance and durability.
Laminated Veneer Lumber (LVL) lintels have become increasingly popular in recent years due to their strength and versatility. They are made by bonding thin layers of wood veneers together with adhesives, which makes them stronger than traditional timber lintels. LVL lintels are often used in both residential and commercial construction projects.
In residential construction, LVL lintels are commonly used for supporting the weight of masonry or brickwork above doors and windows. They are also used for load-bearing walls, beams, and headers. LVL lintels are ideal for these applications because they are strong, lightweight, and easy to install. They are also resistant to warping, splitting, and shrinking, which makes them ideal for use in areas with high humidity or moisture.
In commercial construction, LVL lintels are often used for large openings such as garage doors, storefronts, and curtain walls. They are also used for load-bearing walls, beams, and headers. LVL lintels are ideal for these applications because they can span long distances without the need for intermediate support. This makes them ideal for use in large commercial buildings such as shopping centers, office buildings, and warehouses.
LVL lintels are also used in the construction of bridges, tunnels, and other infrastructure projects. They are ideal for these applications because they are strong, lightweight, and easy to transport. They are also resistant to moisture and corrosion, which makes them ideal for use in harsh environments.
In summary, LVL lintels are a versatile and reliable choice for both residential and commercial construction projects. They are strong, lightweight, and easy to install, making them ideal for a wide range of applications.
When it comes to constructing buildings, it is important to adhere to building codes and standards to ensure safety and durability. This is particularly true when it comes to lintels, which are structural elements that support the weight of the wall above an opening.
The International Building Code (IBC) is a model building code developed by the International Code Council (ICC) that is widely used in the United States. The IBC provides requirements for the design and construction of buildings, including the use of lintels.
According to the IBC, lintels must be designed and installed in accordance with accepted engineering practice. This includes ensuring that the lintel is strong enough to support the weight of the wall above the opening, as well as any additional imposed loads.
The IBC also provides specifications for the materials that can be used for lintels. For example, laminated veneer lumber (LVL) lintels must meet the requirements of the American Lumber Standard Committee (ALSC) and be marked with the grade of the lumber used.
In addition to the IBC, local building codes and regulations may also apply to the design and installation of lintels. These regulations may vary depending on the location of the building, as well as the type of building and its intended use.
It is important to consult with local authorities to ensure that the design and installation of your lintels meet all applicable codes and regulations. Failure to do so can result in costly fines and delays, as well as potential safety hazards.
In summary, building codes and standards are an important consideration when it comes to the design and installation of lintels. By adhering to these codes and regulations, you can ensure the safety and durability of your building, as well as avoid potential legal and financial consequences.
When it comes to LVL lintels, proper maintenance is essential to ensure their longevity and structural integrity. In this section, we will cover some of the key practices and factors that can help you maintain the durability of your LVL lintels.
Regular inspection of your LVL lintels is crucial to identify any signs of damage or deterioration. You should inspect your lintels at least once a year and after any significant weather events or seismic activity. During the inspection, look for signs of cracking, warping, twisting, or sagging. If you notice any of these signs, you should contact a professional to assess the lintel’s condition and recommend the appropriate repairs.
Several factors can affect the longevity of your LVL lintels. One of the most critical factors is exposure to moisture. Moisture can cause the LVL lintel to swell, warp, or rot over time. To minimize the impact of moisture, make sure your lintels are adequately protected from the elements. You can do this by installing a waterproof membrane or a suitable coating on the lintel’s surface.
Another factor that can affect the longevity of your LVL lintels is the load capacity. Overloading the lintel can cause it to bend or sag, compromising its structural integrity. To avoid overloading, make sure you know the maximum load capacity of your LVL lintel and never exceed it.
Finally, the quality of the installation can also affect the longevity of your LVL lintels. Improper installation can cause the lintel to shift or settle over time, leading to structural issues. Make sure you hire a professional contractor with experience in installing LVL lintels to ensure a proper installation.
In summary, regular inspections, minimizing exposure to moisture, avoiding overloading, and proper installation are critical factors in maintaining the durability of your LVL lintels.
If you are interested in any of our products or would like to discuss a customized order, Please feel free to contact us.