Leading Film Faced Plywood Manufacturing
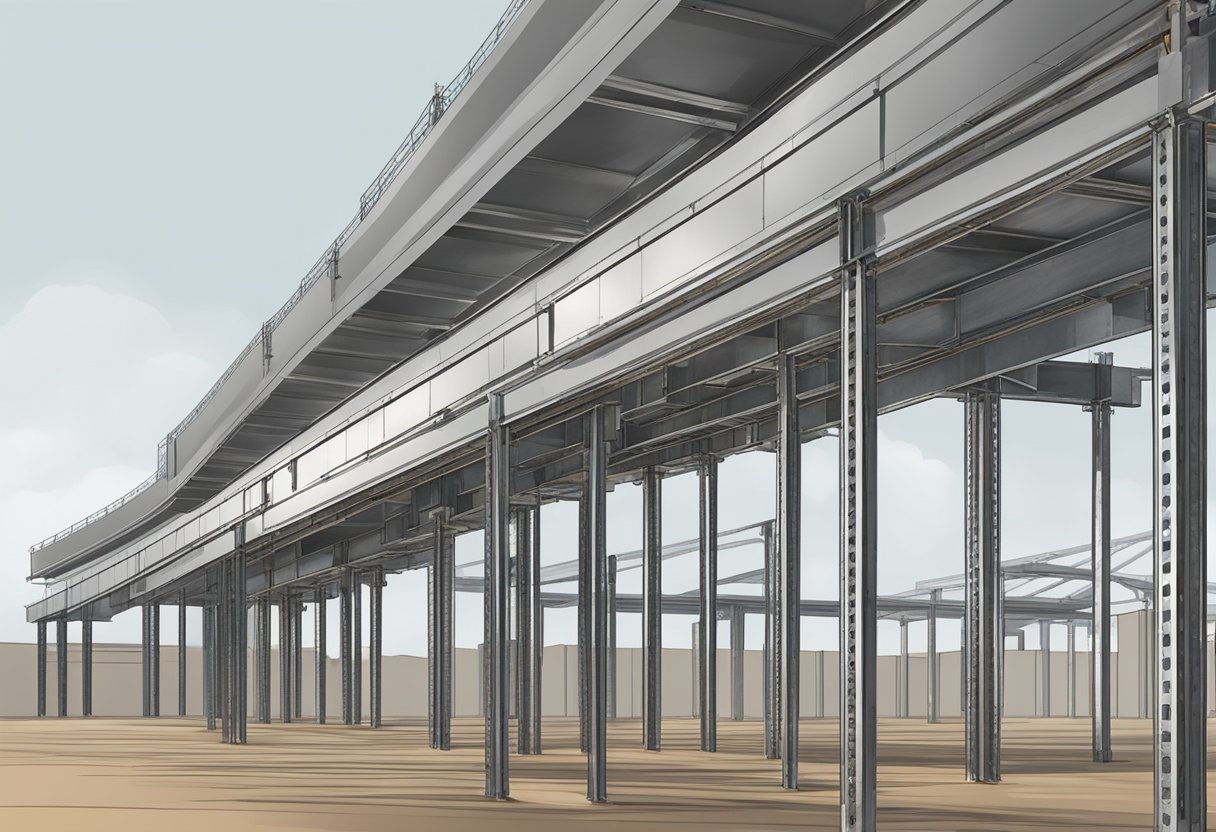
Leading Film Faced Plywood Manufacturing
If you are looking for a strong and durable beam for your construction project, then you might want to consider using a laminated veneer lumber (LVL) beam, commonly known as a “lam beam.” LVL beams are engineered wood products that are made by gluing together multiple layers of thin wood veneers. The resulting product is stronger, more stable, and more uniform than traditional solid-sawn lumber.
Lam beams are widely used in the construction industry for a variety of applications, such as headers, beams, rim boards, and edge-forming material. They are particularly popular for long-span applications, such as floor joists and roof rafters, where their superior strength and stiffness allow for greater design flexibility and reduced construction costs. Additionally, LVL beams are less prone to warping, twisting, and splitting than traditional lumber, which can result in more stable and durable structures.
Lam beams, or laminated veneer lumber beams, are made of multiple layers of thin wood veneers that are glued together with a strong adhesive. The veneers are typically arranged with the wood grain in each layer running in the same direction, which gives the beam its strength. The adhesive used in the manufacturing process is typically a formaldehyde-based resin, which is known for its high bonding strength and durability.
The wood used to make lam beams is typically sourced from fast-growing trees, such as pine or spruce, which are sustainably harvested from managed forests. This makes lam beams a more environmentally friendly option than traditional solid wood beams, which are often made from old-growth trees that take decades to replace.
When designing a structure that will use lam beams, it is important to consider the load that the beams will need to support. Lam beams are typically stronger than solid wood beams of the same dimensions, but their strength can still be affected by factors such as the length of the beam, the spacing between supports, and the type of load that will be placed on the beam.
To ensure that your lam beam structure is safe and structurally sound, it is important to consult with a qualified engineer or architect who can help you select the appropriate beam size and spacing for your specific application. They will also be able to help you determine the appropriate fasteners and connectors to use with your lam beams, as well as any additional support structures that may be necessary to ensure the safety and stability of your structure.
Overall, lam beams are a versatile and durable building material that can be used in a wide range of applications, from residential construction to commercial and industrial projects. By understanding the fundamentals of lam beam design and construction, you can ensure that your structure is safe, stable, and built to last.
LAM (Laser Additive Manufacturing) is a process that uses a laser beam to melt and solidify the material in a powder bed according to slices of a corresponding three-dimensional computer aided design (3D-CAD) model. There are several manufacturing processes involved in LAM.
In the first step of the LAM process, the metal powder is spread evenly on the substrate. The powder is then glued to the substrate using a binding agent. The binding agent is applied in a thin layer to ensure that the powder is evenly distributed. The substrate is then pressed to ensure that the powder is firmly attached to the substrate. The pressing process helps to eliminate any air pockets that may be present in the powder.
After the powder has been glued and pressed onto the substrate, the next step is to cure the binding agent. The curing process is usually done in an oven at a temperature of around 200 degrees Celsius. The curing process helps to strengthen the bond between the powder and the substrate. Once the curing process is complete, the substrate is ready for the LAM process.
The final step in the LAM process is finishing. Finishing involves removing any excess powder that may be present on the surface of the substrate. This is done using a brush or any other tool that can remove the excess powder without damaging the substrate. The finished product is then ready for use.
In conclusion, the LAM process involves several manufacturing processes such as gluing, pressing, curing, and finishing. Each of these processes plays a crucial role in ensuring that the final product is of high quality. The LAM process has revolutionized the manufacturing industry by providing a faster and more efficient way of producing high-quality metal parts.
When it comes to structural applications, laminated beams (lam beams) offer a versatile and reliable solution for both residential and commercial construction projects.
In residential construction, lam beams are commonly used as headers, beams, and columns. They provide a strong and durable support system for roofs, floors, and walls. Lam beams can also be used to create open floor plans, allowing for larger living spaces without the need for additional support columns or walls.
One of the advantages of using lam beams in residential construction is their ability to span longer distances than traditional solid wood beams. This means that fewer columns or walls are needed, resulting in more open space and greater design flexibility. Lam beams are also available in a variety of sizes and shapes, making them suitable for a wide range of residential applications.
In commercial construction, lam beams are a popular choice for a variety of applications, including roofs, floors, and bridges. They are often used in large-scale projects, such as sports arenas and convention centers, where their strength and versatility make them an ideal choice.
Lam beams can also be used in commercial buildings to create unique and visually appealing designs. They can be curved or shaped to fit specific design requirements, and they can be left exposed to create a natural and warm aesthetic.
In addition to their strength and versatility, lam beams are also an environmentally friendly choice for commercial construction. They are made from renewable resources and can be recycled at the end of their useful life.
Overall, lam beams offer a reliable and versatile solution for both residential and commercial construction projects. Their strength, durability, and design flexibility make them a popular choice for architects and builders alike.
When it comes to building construction, performance characteristics are essential to consider. Laminated beams, or lam beams, are engineered wood products that have excellent performance characteristics. They are made by bonding multiple layers of wood together using adhesives, creating a strong and durable structural component. Here are some of the performance characteristics of lam beams that make them an excellent choice for construction:
Lam beams have a high load-bearing capacity, which means they can support heavy loads without bending or breaking. The load-bearing capacity of lam beams depends on the size and grade of the beam. The larger the beam, the higher the load it can support. Lam beams are available in a variety of sizes and grades, making them suitable for a wide range of construction applications.
Lam beams are highly durable and require minimal maintenance. They are resistant to warping, twisting, and shrinking, which means they maintain their shape and structural integrity over time. They are also resistant to decay, rot, and insect damage, which makes them an excellent choice for outdoor construction projects. Additionally, they require minimal maintenance, making them a cost-effective choice for construction projects.
In conclusion, the performance characteristics of lam beams make them an excellent choice for construction. They have a high load-bearing capacity, are highly durable, and require minimal maintenance. If you are looking for a strong and reliable structural component for your construction project, lam beams are a great choice.
When it comes to installing laminated beams (glulam), it’s important to follow best practices to ensure the beams perform as designed. Here are some tips to help you install glulam beams correctly:
Before installing a glulam beam, make sure you have the right size and type of beam for your project. Be sure to consult with a structural engineer or other qualified professional to determine the appropriate size and type of beam for your project.
Glulam beams are engineered components and should be handled with care during installation. Avoid dropping, dragging, or throwing the beams, as this can damage the structural integrity of the beam.
When installing glulam beams, it’s important to use proper fasteners. Nails and screws should be long enough to penetrate the beam and the supporting structure. Use galvanized or stainless steel fasteners to prevent corrosion.
Follow the manufacturer’s guidelines for installing glulam beams. These guidelines will provide specific instructions for handling, storing, and installing the beams.
Glulam beams can absorb moisture, which can cause them to swell or shrink. Be sure to store the beams in a dry location before installation. During installation, use shims to allow for any necessary adjustments due to moisture content.
By following these best practices, you can ensure that your glulam beams perform as designed and provide a durable and long-lasting solution for your project.
If you are interested in any of our products or would like to discuss a customized order, Please feel free to contact us.