Leading Film Faced Plywood Manufacturing
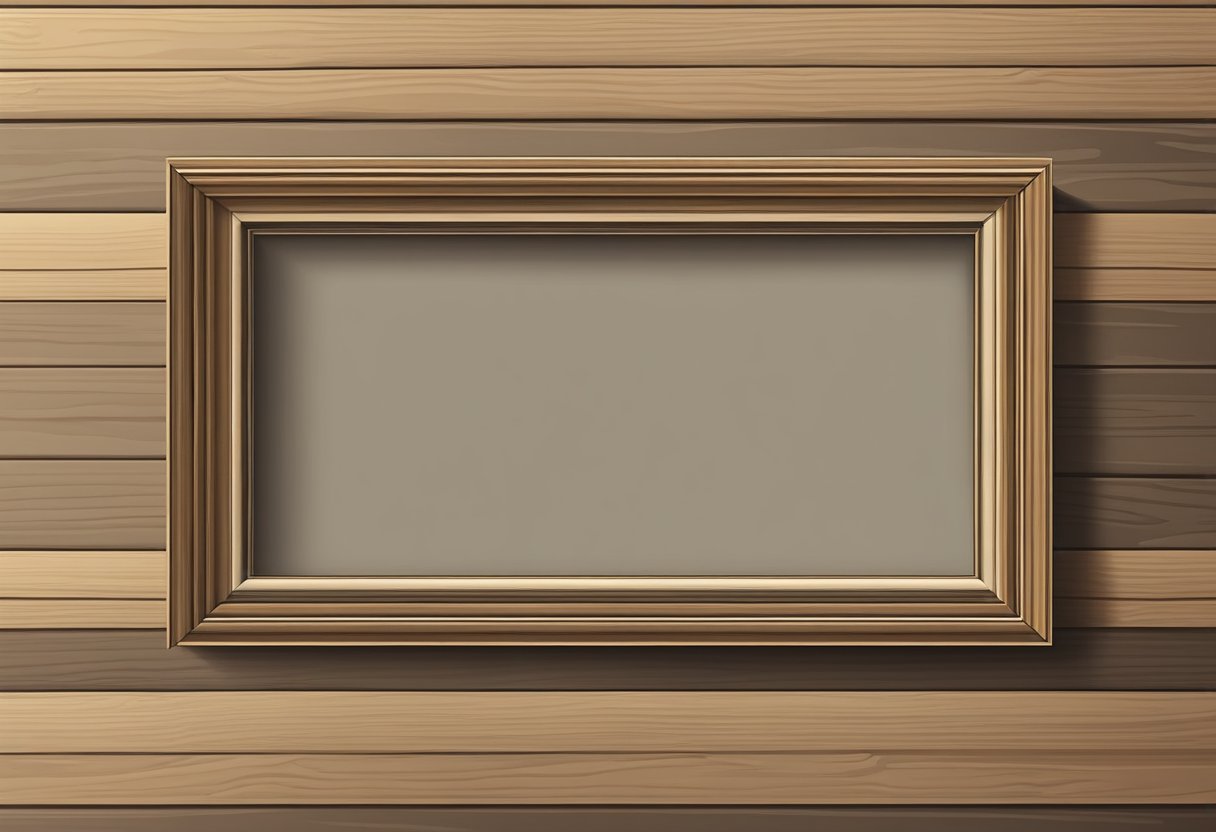
Leading Film Faced Plywood Manufacturing
If you’re in the construction industry, you’ve probably heard of Laminated Veneer Lumber (LVL). LVL is an engineered wood product that is used for a variety of applications, including headers, beams, rimboards, and edge-forming material. LVL is made by bonding thin wood veneers together with adhesives under heat and pressure, resulting in a strong and stable product that is resistant to warping and splitting.
One of the main advantages of LVL is its strength. According to Fine Homebuilding, LVL combines the versatility of sawn lumber with the strength of engineered beams. This makes it an ideal choice for carrying beams and floor framing. In addition to its strength, LVL is also straighter and more uniform than typical milled lumber, making it easier to work with and resulting in a more consistent finished product.
Another advantage of LVL is its versatility. LVL can be used for a variety of applications, including residential and commercial construction, as well as for industrial and agricultural buildings. It can be used for load-bearing walls, roof framing, and floor framing, and is available in a range of sizes and lengths to meet the needs of any project. Whether you’re building a small addition to your home or a large commercial building, LVL is a versatile and reliable choice for your framing needs.
When designing a frame using Laminated Veneer Lumber (LVL), there are several key factors to consider. These include the materials and properties of LVL, structural analysis, and load distribution.
LVL is a high-strength engineered wood product made from layers of thin wood veneers glued together. It is known for its strength, stiffness, and dimensional stability. LVL is available in a variety of thicknesses and grades, and its properties can be customized to meet specific design requirements.
The strength of LVL is determined by its modulus of elasticity (MOE) and modulus of rupture (MOR). MOE refers to the stiffness of the material, while MOR refers to its maximum bending strength. These properties can be affected by factors such as the thickness of the veneers, the type of adhesive used, and the orientation of the grain.
Structural analysis is an essential part of designing a frame using LVL. This involves determining the loads that the frame will be subjected to and ensuring that the LVL members are sized and spaced appropriately to resist these loads.
LVL is typically used in applications where high strength and stiffness are required, such as in beams, headers, and columns. When designing a frame using LVL, it is important to consider the span of the members, the spacing between them, and the type of connection used.
Load distribution is another important consideration when designing a frame using LVL. This involves ensuring that the loads are distributed evenly across the members to prevent overloading and failure.
One way to achieve even load distribution is to use blocking or bridging between the members. This involves placing additional pieces of LVL between the main members to distribute the load and increase the stiffness of the frame.
In summary, designing a frame using LVL requires careful consideration of the materials and properties of LVL, structural analysis, and load distribution. By taking these factors into account, you can create a strong and durable frame that will provide reliable performance for years to come.
When it comes to framing, there are several types of frame levels that you can choose from. Each type has its own unique features and advantages. In this section, we will discuss the three most common types of frame levels: Rigid Frame, Braced Frame, and Portal Frame.
A Rigid Frame is a type of frame that is designed to resist bending and twisting. It is made up of a series of beams and columns that are connected together with rigid joints. This type of frame is commonly used in buildings that require a high degree of stability, such as industrial buildings, warehouses, and factories.
A Braced Frame is a type of frame that is designed to resist lateral loads. It is made up of a series of beams and columns that are connected together with diagonal braces. This type of frame is commonly used in buildings that are located in areas that are prone to earthquakes or high winds.
A Portal Frame is a type of frame that is designed to resist both bending and twisting. It is made up of a series of beams and columns that are connected together with moment-resisting connections. This type of frame is commonly used in buildings that require a high degree of stability, such as multi-story buildings and bridges.
In summary, when choosing a frame level, it is important to consider the specific needs of your project. Each type of frame level has its own unique features and advantages, so it is important to choose the one that is best suited for your particular application.
Joinery and connections are critical to the strength and stability of LVL framing. The most common joinery techniques for LVLs include butt joints, scarf joints, and finger joints. Butt joints are the simplest and most commonly used technique, but they are also the weakest. Scarf joints are stronger and are commonly used for longer spans. Finger joints are the strongest and are used for the longest spans.
When it comes to connections, there are several options available. The most common connection technique is the use of metal plates or brackets. These are easy to install and provide a strong connection. Another option is the use of bolts or screws. These are more time-consuming to install but provide a stronger connection.
Erection and assembly of LVL framing requires careful planning and execution. Before assembly, it is important to ensure that all components are properly sized and cut to length. Once the pieces are ready, assembly can begin.
The first step is to lay out the framing plan and mark the locations of all the components. Next, the pieces are assembled using the chosen joinery technique and connected using the chosen connection technique.
During assembly, it is important to ensure that all components are level and plumb. This can be achieved using a level and a plumb bob. Once assembly is complete, the framing should be checked for squareness to ensure that it is structurally sound.
In conclusion, proper joinery and connection techniques, as well as careful planning and execution during erection and assembly, are critical to the strength and stability of LVL framing. By following these guidelines, you can ensure that your LVL framing is strong and stable, providing a solid foundation for your construction project.
When designing with Laminated Veneer Lumber (LVL), there are several considerations to keep in mind. These include aesthetic elements, functional requirements, and building codes and standards.
LVL can be customized to fit the aesthetic needs of any project. The veneers used in LVL can be selected for their color and grain pattern, and the surface can be sanded to provide a smooth finish. LVL can also be painted or stained to match the desired appearance.
LVL is a strong and durable material that can handle heavy loads. When designing with LVL, it is important to consider the intended use of the structure and the load requirements. LVL can be designed to span long distances without the need for intermediate supports, making it ideal for open-concept designs.
When designing with LVL, it is important to follow building codes and standards. LVL is recognized by the International Building Code (IBC) and can be used in fire-resistance-rated wall assemblies listed in the IBC. However, additional design and construction considerations may be required. It is important to consult with the manufacturer’s evaluation and product reports to ensure compliance with building codes and standards.
In addition, LVL can be designed to meet specific performance requirements, such as wind and seismic loads. It is important to consult with a structural engineer to ensure that the LVL design meets the required performance criteria.
Overall, LVL is a versatile and reliable material that can be customized to meet the aesthetic and functional needs of any project. By considering the aesthetic elements, functional requirements, and building codes and standards, you can design with LVL with confidence.
Laminated Veneer Lumber (LVL) is a versatile and durable building material that has been used in a variety of applications. Here are a few case studies and examples of how LVL has been used in different projects:
LVL is an excellent choice for residential construction projects due to its strength and versatility. It can be used for floor joists, roof rafters, and beams. In a case study by Fine Homebuilding, LVLs were used as the backbone for floor framing, allowing for the assembly of big beams without a big crew. The laminated veneer lumber combines the versatility of sawn lumber with the strength of engineered beams.
LVL is also a popular choice for commercial construction projects. In a case study by Architecture and Design, Hyne Timber’s LVL E-Beam+ (F17) was used as an engineered timber alternative to F17 hardwood. It has a high strength to weight ratio, making it an ideal choice for large commercial buildings.
LVL is commonly used for portal frames in construction projects. In a case study by Futurebuild, the hyFRAME LVL kitset portal frame solution was used as part of a total build system. The prefabricated timber portal frames were designed for use in a variety of commercial and residential construction projects.
Overall, LVL is a versatile and durable building material that can be used in a variety of applications. Its strength, versatility, and ease of use make it an ideal choice for both residential and commercial construction projects.
If you are interested in any of our products or would like to discuss a customized order, Please feel free to contact us.