Leading Film Faced Plywood Manufacturing
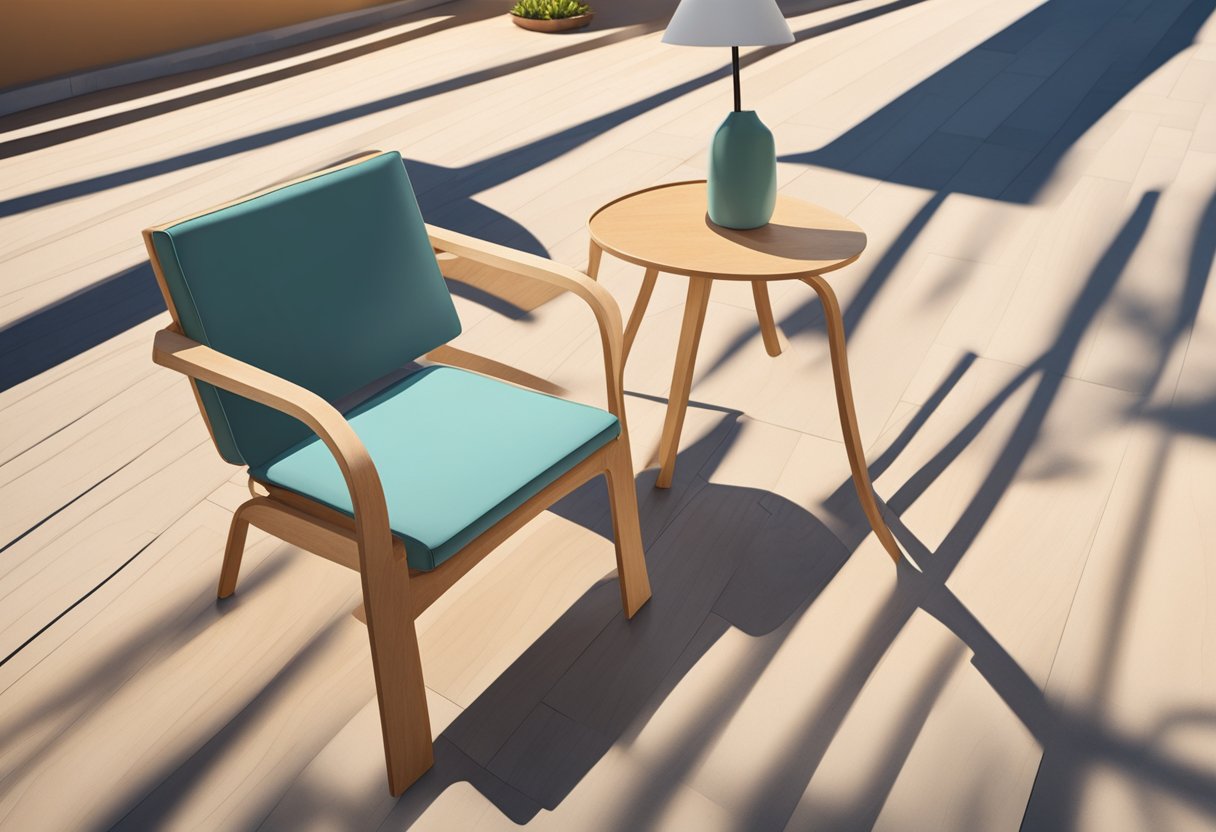
Leading Film Faced Plywood Manufacturing
If you’re looking for a versatile and flexible material for your next woodworking project, curved plywood might be just what you need. Unlike traditional flat plywood, curved plywood is designed to bend and conform to different shapes and contours, making it ideal for creating unique and eye-catching furniture pieces, cabinetry, and architectural features.
Curved plywood is made by laminating thin layers of wood veneer together with the grain running in different directions. This cross-grain construction gives the plywood its flexibility and allows it to bend and curve without cracking or breaking. It can be used to create a wide range of shapes and forms, from simple curves to complex and intricate designs.
One of the main advantages of curved plywood is its versatility. It can be used in a variety of applications, from furniture making to architectural design. It’s also available in different sizes, thicknesses, and grades, making it easy to find the right type of plywood for your specific project. Whether you’re looking to create a curved wall, a curved ceiling, or a unique piece of furniture, curved plywood can help you achieve your design goals with ease.
Curved plywood has a rich history that dates back centuries. Over time, the manufacturing process has evolved, and today, curved plywood is used in a wide range of applications, from furniture to architecture.
The origins of curved plywood can be traced back to ancient Egypt, where wooden boards were glued together to create composite materials. Early civilizations used similar techniques to strengthen and waterproof their structures.
In the 19th century, plywood began to evolve as a material. It was used to create curved surfaces, and manufacturers began to experiment with different techniques to create more complex shapes. One of the most significant developments during this time was the invention of the rotary lathe, which allowed for the creation of thin, flexible sheets of plywood.
Today, curved plywood is used in a variety of applications, from furniture and cabinetry to architecture and design. Modern advancements in manufacturing techniques have made it possible to create even more complex shapes and designs using curved plywood.
One of the most significant advancements in recent years has been the use of computer-aided design (CAD) and computer-aided manufacturing (CAM) technologies. These technologies allow for highly precise and complex designs to be created and manufactured with ease.
Another recent development has been the use of 3D printing technology to create curved plywood prototypes. This technology allows designers to create and test complex shapes and designs quickly and efficiently.
Overall, the history of curved plywood is a fascinating one, and the material continues to evolve and be used in new and innovative ways.
If you are interested in using curved plywood for your next project, it’s important to understand the manufacturing process. The process involves several steps that are crucial in achieving a high-quality end product.
The first step in the manufacturing process is veneer selection. Veneer is a thin layer of wood that is peeled from a log. The quality of the veneer is important because it affects the strength and durability of the final product. The veneer is typically chosen based on its thickness and grain pattern. The thickness of the veneer is important because it affects the flexibility of the plywood. The grain pattern is important because it affects the appearance of the final product.
Once the veneer is selected, the next step is bonding. Adhesives are used to bond the veneer together to create the plywood. The type of adhesive used is important because it affects the strength and durability of the final product. There are several types of adhesives that can be used, including phenol-formaldehyde, melamine-urea-formaldehyde, and polyurethane. Each type of adhesive has its own advantages and disadvantages.
The final step in the manufacturing process is pressing. Pressing is the process of applying heat and pressure to the veneer to bond it together. The pressing technique used is important because it affects the shape and flexibility of the plywood. There are several pressing techniques that can be used, including hot pressing, cold pressing, and vacuum pressing. Each technique has its own advantages and disadvantages.
In summary, the manufacturing process of curved plywood involves veneer selection, adhesive and bonding, and pressing techniques. Each step is important in achieving a high-quality end product. By understanding the manufacturing process, you can make informed decisions when choosing curved plywood for your next project.
Curved plywood is a versatile material that has revolutionized the design industry. It has opened up new possibilities for furniture, architecture, and even automotive and aviation design. Here are some of the most popular uses of curved plywood:
Curved plywood has become a popular choice for furniture designers because of its flexibility and durability. It can be bent into a variety of shapes and curves, making it ideal for creating unique and eye-catching designs. From chairs and tables to cabinets and shelves, curved plywood can add a touch of elegance and sophistication to any piece of furniture.
Curved plywood is also widely used in architecture. It can be used to create curved walls, ceilings, and even roofs. This makes it an ideal material for creating unique and visually stunning buildings. Curved plywood can also be used to create decorative elements such as arches, columns, and balustrades.
Curved plywood has also found its way into the automotive and aviation industries. It is used to create lightweight and durable parts for cars, planes, and even boats. Curved plywood can be used to create everything from dashboards and steering wheels to airplane wings and boat hulls.
Curved plywood is a versatile and flexible material that has opened up new possibilities for designers in a variety of industries. From furniture and architecture to automotive and aviation, curved plywood has proven to be a reliable and durable material that can add a touch of elegance and sophistication to any design.
Curved plywood has been around for decades, but recent technological innovations have made it more accessible and practical for designers and manufacturers. In this section, we will discuss two major technological innovations that have transformed the use of curved plywood in modern design: CNC machining and 3D modeling.
CNC (Computer Numerical Control) machining has revolutionized the production of curved plywood. It allows for precise and efficient cutting of intricate shapes and curves, which was previously difficult and time-consuming. With CNC machining, designers can create complex and unique designs that would have been impossible to produce with traditional methods.
CNC machining has also made it easier to produce curved plywood in large quantities. It eliminates the need for manual labor, which reduces the risk of errors and inconsistencies in the final product. This technology has made curved plywood more affordable and accessible for commercial applications, such as furniture and interior design.
Another technological innovation that has transformed the use of curved plywood is 3D modeling. With 3D modeling software, designers can create virtual models of their designs and test them for feasibility and functionality before production. This allows for more efficient and cost-effective design iterations, reducing the risk of errors and waste.
3D modeling also allows for more precise and accurate designs, which can be translated directly to CNC machines for production. This technology has made it easier for designers to experiment with different shapes and curves, and to create complex and unique designs that would have been difficult to produce with traditional methods.
Technological innovations such as CNC machining and 3D modeling have transformed the use of curved plywoods in modern design. They have made it more accessible, practical, and cost-effective, allowing designers to create complex and unique designs that were previously impossible to produce.
When it comes to curved plywoods, the environmental impact is an important consideration. In this section, we’ll explore the sustainability practices and recycling and reuse options for curved plywoods.
Curved plywoods can be made using a variety of wood species, and the sustainability of the wood used is a key factor in the environmental impact of the material. Many manufacturers use wood from sustainably managed forests, which ensures that the wood is harvested in a way that maintains the health and productivity of the forest ecosystem.
Additionally, many manufacturers use adhesives that are free from formaldehyde, a chemical that can have negative health effects and is harmful to the environment. By using low-VOC and formaldehyde-free adhesives, manufacturers can reduce the environmental impact of curved plywoods.
Curved plywood can be recycled and reused in several ways. For example, it can be ground up and used as a component in composite wood products, such as particleboard. Additionally, it can be used as fuel for energy production, which can help reduce the use of fossil fuels.
Another option for recycling and reusing curveds plywood is to repurpose it into new products. For example, curved plywoods can be used to create furniture, architectural elements, and even art. By repurposing curved plywoods, you can extend its lifespan and reduce the amount of waste that ends up in landfills.
Overall, curved plywoods can be a sustainable and environmentally friendly material when produced and used responsibly. By choosing curveds plywood made from sustainably managed wood and using low-VOC and formaldehyde-free adhesives, you can help reduce the environmental impact of your project. And by recycling and reusing curveds plywood, you can extend its lifespan and reduce waste.
1. What is curved plywood, and how is it different from traditional plywood? Curved plywood is a versatile material designed to bend and conform to various shapes and contours, unlike traditional flat plywood. It’s made by laminating thin layers of wood veneer with the grain running in different directions, giving it flexibility without cracking.
2. What are the advantages of using curved plywood? Curved plywood offers versatility in design, making it suitable for a wide range of applications such as furniture making and architectural design. Its availability in different sizes, thicknesses, and grades makes it adaptable to various projects.
3. Can you provide a brief history of curved plywood? Curved plywood has roots dating back to ancient Egypt, where wooden boards were glued together for composite materials. In the 19th century, advancements like the rotary lathe enabled the creation of thin, flexible plywood. Today, modern technologies like CAD/CAM and 3D printing have further expanded its possibilities.
4. What is the manufacturing process of curved plywoods? The process involves veneer selection, adhesive bonding, and pressing techniques. Veneer selection is crucial for strength and appearance, while various adhesives like phenol-formaldehyde are used for bonding. Pressing techniques such as hot pressing ensure the plywood retains its desired shape and flexibility.
5. How is curved plywoods used in design and applications? Curved plywood finds applications in furniture design, architecture, automotive, and aviation industries. It can be molded into various shapes for chairs, tables, curved walls, ceilings, and even lightweight parts for vehicles and aircraft.
If you are interested in any of our products or would like to discuss a customized order, Please feel free to contact us.