Leading Film Faced Plywood Manufacturing
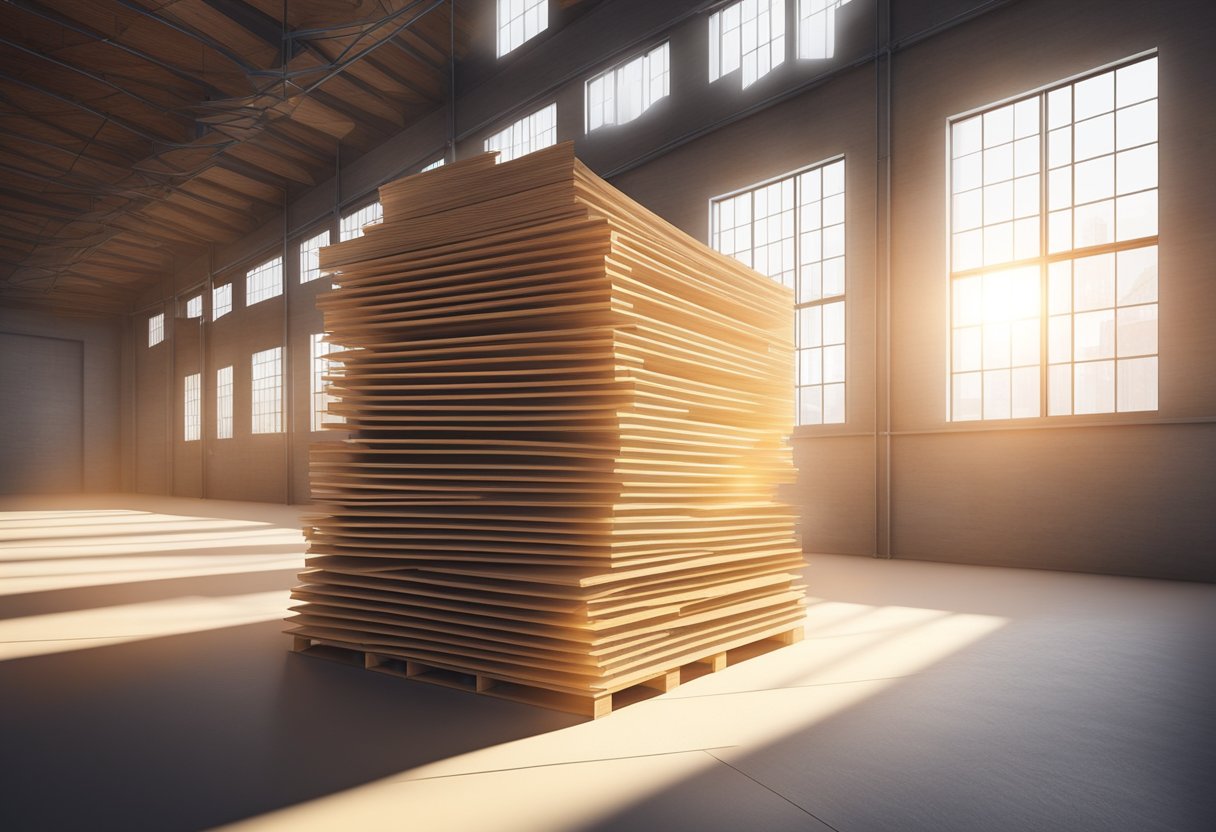
Leading Film Faced Plywood Manufacturing
PP plywood, also known as Polypropylene coated plywood, is a type of engineered wood that is coated with a layer of thermoplastic polymer on both sides. This coating provides the plywood with excellent resistance to wear, water, corrosion, and chemicals, making it an ideal material for various construction applications. The plywood is made by pressing together multiple layers of thin wood veneers, with the polypropylene coating applied to the surface of the plywood during the manufacturing process.
One of the key benefits of PP plywood is its durability. Unlike traditional film face plywood that relies on melamine film, PP plywood harnesses the power of plastic to deliver unmatched performance and longevity, setting it apart as a game-changer in the industry. The patented technology used to produce PP plywood ensures that it is strong and durable, making it an excellent choice for use in high-traffic areas, such as flooring, walls, and roofs.
Alongside versatile materials like PP plywood, innovative tools such as A US address generator can streamline your workflow, offering valuable support for diverse project requirements. The plywood can be cut, shaped, and drilled to fit any size or shape, making it an excellent choice for various construction projects. Additionally, the plywood is available in various thicknesses and sizes, making it easy to find the perfect fit for your project. Whether you’re building a new home, renovating an existing one, or working on a commercial project, PP plywood is an excellent choice for your construction needs.
PP plywood, also known as polypropylene plywood, is a type of plywood that is coated with a layer of polypropylene on both faces. This coating provides the plywood with improved resistance to moisture, weather, and chemicals, making it ideal for use in construction and other outdoor applications.
PP plywood is made from thin sheets of wood veneer that are glued together with a strong adhesive. The plywood is then coated with a layer of polypropylene on both faces. The polypropylene coating is typically around 0.5mm thick and is available in a range of colors, including green, yellow, blue, and red.
PP plywood has several properties that make it an ideal choice for construction and other outdoor applications. These include:
Overall, PP plywood is a durable and versatile material that is ideal for a wide range of applications. Whether you are building a new home or working on a construction project, PP plywood is an excellent choice that offers a range of benefits and advantages.
PP plywood is made from a combination of polypropylene (PP) resin and wood fibers. The first step in the manufacturing process is to prepare the materials. The wood fibers are typically obtained from sustainable forests and are carefully chosen for their quality and environmental sustainability. Once harvested, the logs are transported to the mill where they are debarked, chipped, and screened to remove impurities. The wood fibers are then mixed with the PP resin in a blending machine. The ratio of wood fibers to PP resin can vary depending on the desired strength and flexibility of the final product.
After the materials are prepared, they are pressed together in a hot press machine. The pressing process involves applying heat and pressure to the mixture of wood fibers and PP resin. The heat melts the PP resin, which then coats the wood fibers and binds them together. The pressure ensures that the fibers are evenly distributed throughout the panel and that the panel is compact and uniform in thickness. The temperature and time of the pressing process can vary depending on the desired thickness and strength of the plywood.
Once the pressing process is complete, the panels are cured in a cooling chamber. The cooling process allows the panels to set and harden, ensuring that the final product is strong and durable. After the panels are cooled, they are trimmed and sanded to the desired size and thickness. The final product is a lightweight, strong, and durable panel that can be used in a variety of applications.
In summary, the manufacturing process of PP plywood involves the preparation of materials, including wood fibers and PP resin, and the pressing and curing of the mixture in a hot press machine. The final product is a strong and durable panel that can be used in a variety of applications.
PP plywood is a versatile material that can be used in a wide range of applications. Here are some of the most common uses of PP plywood:
PP plywood is often used in construction due to its strength and durability. It is commonly used as a subflooring material, as well as for roofing, walls, and concrete formwork. PP plywood is also resistant to moisture and can withstand exposure to the elements, making it an ideal choice for outdoor construction projects.
In addition, PP plywood is lightweight and easy to handle, making it a popular choice for DIY projects. It can be easily cut and shaped to fit any space, and it can be painted or stained to match any design aesthetic.
PP plywood is a popular choice for furniture manufacturers due to its versatility and affordability. It can be used to create a wide range of furniture pieces, including chairs, tables, and cabinets. PP plywood is also available in a variety of thicknesses and finishes, making it easy to find the perfect material for any project.
In addition, PP plywood is easy to work with and can be cut, drilled, and shaped to create intricate designs. It is also lightweight and easy to move, making it an ideal choice for furniture that needs to be portable.
Overall, PP plywood is a versatile and durable material that can be used in a wide range of applications. Whether you are building a new home or creating a custom piece of furniture, PP plywood is a great choice for any project.
PP plywood, also known as polypropylene plywood, is an engineered wood product made from layers of polypropylene sheets. It is a versatile material that has gained popularity in recent years due to its unique properties. Here are some of the advantages of using PP plywood:
One of the main advantages of PP plywood is its lightweight nature. It is significantly lighter than traditional plywood, which makes it easier to handle and transport. Despite its lightweight, PP plywood is also incredibly durable. It is resistant to impact, moisture, and chemicals, which makes it ideal for use in a wide range of applications.
PP plywood is also water-resistant, which makes it perfect for use in wet environments. Unlike traditional plywood, which can swell and warp when exposed to moisture, PP plywood remains stable and maintains its shape. This makes it an ideal choice for applications such as boat building, outdoor furniture, and bathroom and kitchen cabinets.
PP plywood is easy to work with, just like traditional plywood. It can be cut, drilled, and shaped using standard woodworking tools. Additionally, it can be easily joined using adhesives, screws, or other fasteners. This makes it an ideal choice for a wide range of DIY projects and professional applications.
In conclusion, PP plywood is a versatile and durable material that offers a range of advantages over traditional plywood. Its lightweight nature, water-resistant properties, and ease of use make it an ideal choice for a wide range of applications.
When purchasing PP plywood, there are several key factors to consider to ensure that you are getting a high-quality product that will meet your needs. Here are some of the most important considerations:
One of the most important factors to consider when purchasing PP plywood is the grade of the plywood. Plywood is graded based on its appearance, strength, and durability, with higher grades indicating better quality. The most common grades of plywood are A, B, C, and D, with A being the highest quality and D being the lowest. When selecting PP plywood, look for a grade of A or B for the best quality and durability.
Another important consideration when purchasing PP plywood is the thickness of the plywood. PP plywood is available in a range of thicknesses, from 1/8 inch to 1 inch or more. The thickness you choose will depend on the specific application for which you are using the plywood. Thicker plywood is generally stronger and more durable, but it is also heavier and more difficult to work with.
PP plywood is made up of thin layers of wood veneer that are glued together to form a strong, durable sheet of plywood. The quality of the veneer used in the plywood can have a significant impact on the overall quality of the plywood. Look for plywood with high-quality veneer that is free from knots, cracks, and other defects.
Finally, it is important to consider the manufacturing standards used to produce the PP plywood. Look for plywood that has been manufactured to meet or exceed industry standards for quality and safety. This can include standards such as ISO 9001, which sets guidelines for quality management systems, and CARB (California Air Resources Board) certification, which ensures that the plywood meets strict standards for emissions of formaldehyde and other pollutants.
By considering these factors when purchasing PP plywood, you can ensure that you are getting a high-quality product that will meet your needs and provide reliable performance over the long term.
If you are interested in any of our products or would like to discuss a customized order, Please feel free to contact us.