Leading Film Faced Plywood Manufacturing
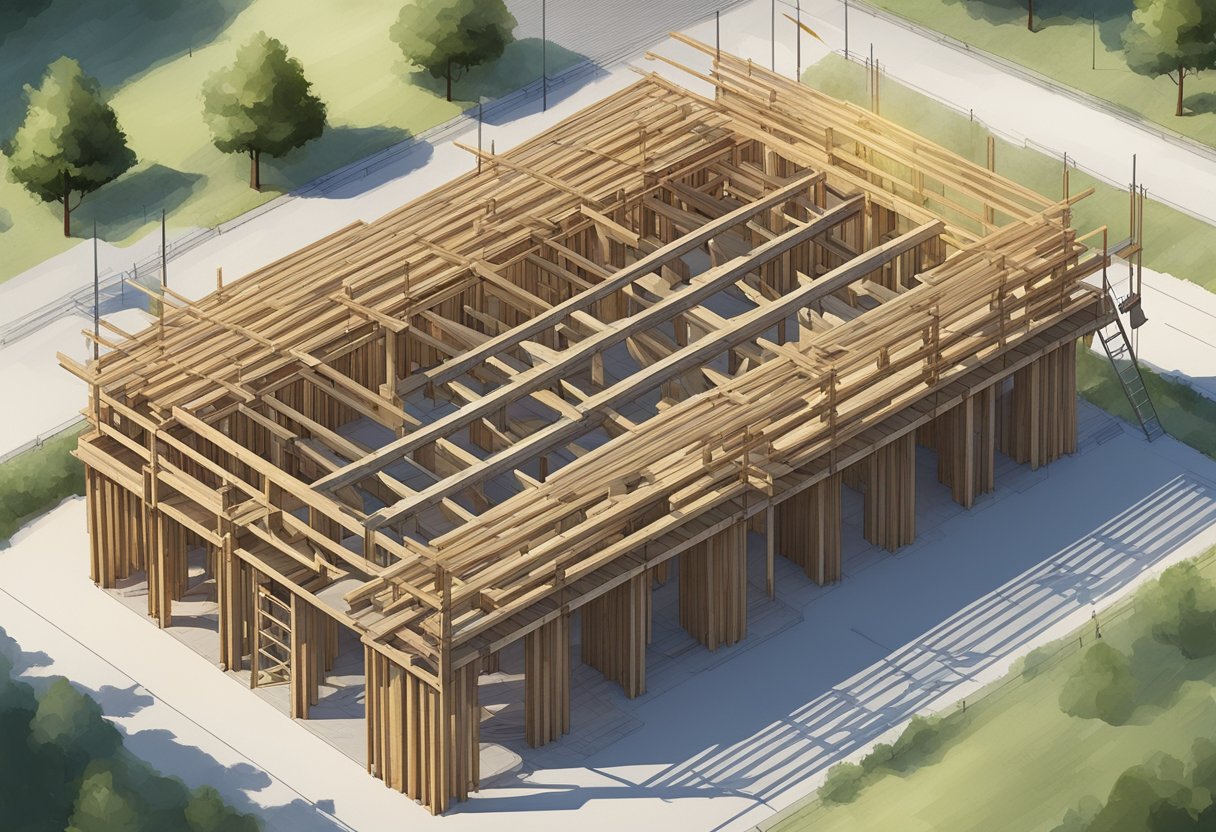
Leading Film Faced Plywood Manufacturing
If you are involved in construction, you have likely heard of formwork LVL, or laminated veneer lumber. LVL is a type of engineered wood product that is used in a variety of construction applications, including formwork, beams, lintels, purlins, truss chords, and more. LVL is a strong, durable, and versatile material that offers many benefits over traditional timber.
One of the main advantages of formwork LVL is its strength. LVL is made by bonding multiple layers of thin wood together, creating a material that is stronger and more stable than traditional timber. This makes LVL an ideal choice for use in structural applications, where strength and durability are essential. Additionally, LVL can be manufactured to almost any length, making it a versatile material that can be used in a wide range of construction projects.
Another advantage of formwork LVL is its cost-effectiveness. While LVL may be slightly more expensive than traditional timber, it offers many benefits that make it a cost-effective choice in the long run. For example, LVL is stronger and more durable than traditional timber, which means that it will last longer and require less maintenance over time. Additionally, LVL is easier to work with than traditional timber, which can save time and money during the construction process.
Formwork LVL (Laminated Veneer Lumber) is a strong and durable engineered wood product used in construction for concrete formwork. It is made from thin layers of wood veneer that are glued together with adhesives and pressed under heat and pressure. Formwork LVL is known for its high load-bearing capacity, which makes it ideal for use in commercial buildings.
Formwork LVL is lighter, straighter, and more uniform than traditional formwork timber, which makes it a cost-effective alternative. It is resistant to warping, splitting, and twisting, which means it can withstand the rigors of construction. Formwork LVL is also moisture-resistant, which makes it suitable for use in wet environments.
The manufacturing process of Formwork LVL involves several steps. First, the logs are debarked and cut into thin veneers. The veneers are then dried and sorted based on their quality. The veneers are coated with adhesive and arranged in a specific pattern to form a billet. The billet is then pressed under heat and pressure to form a solid panel. The panel is then cut to size and sanded to a smooth finish.
The adhesive used in the manufacturing process of Formwork LVL is typically a phenol-formaldehyde resin. This resin is known for its water-resistant properties and its ability to bond well with wood fibers. The resin is also formaldehyde-free, which makes it a safer and more environmentally friendly option.
Formwork LVL is a strong and durable material that is ideal for use in construction for concrete formwork. Its high load-bearing capacity, resistance to warping and moisture, and cost-effectiveness make it a popular choice among builders. The manufacturing process of Formwork LVL involves several steps, including drying, sorting, coating, pressing, cutting, and sanding. The adhesive used in the manufacturing process is typically a water-resistant phenol-formaldehyde resin.
When designing formwork LVL, there are several important considerations to keep in mind to ensure optimal performance. Two key factors to consider are load capacity and deflection criteria.
The load capacity of formwork LVL depends on several factors, including the size and thickness of the LVL, as well as the spacing of the supports. It is important to ensure that the LVL is strong enough to support the weight of the concrete and any additional loads that may be placed on it during construction.
To determine the load capacity of formwork LVL, you can refer to manufacturer specifications or consult with a structural engineer. It is important to ensure that the LVL is not overloaded, as this can lead to structural failure and compromise the safety of the construction site.
Deflection refers to the amount of bending that occurs in the formwork LVL under load. To ensure that the LVL maintains its shape and does not deform excessively, it is important to establish deflection criteria and ensure that the LVL meets these requirements.
Deflection criteria are typically based on the span of the LVL and the amount of load it will be subjected to. For example, a shorter span may allow for greater deflection, while a longer span may require stricter deflection criteria.
When designing formwork LVL, it is important to consider both load capacity and deflection criteria to ensure that the LVL is strong enough to support the weight of the concrete and maintain its shape under load. By following these guidelines, you can ensure that your formwork LVL will perform optimally and contribute to a safe and successful construction project.
Formwork LVL is a versatile engineered wood product used extensively in construction for various applications. From scaffolding to concrete forming, LVL offers durability and sustainability to construction endeavors. Here are some of the ways in which formwork LVL is used in construction:
LVL is an excellent material for scaffolding due to its strength and load-bearing capacity. It is commonly used as a plank for scaffolding systems, providing a stable working platform for workers. The smooth surface of LVL planks also makes it easier to move materials and tools across the scaffolding. Moreover, LVL planks are lightweight, making them easy to handle and transport, reducing the risk of injury.
LVL is an ideal material for concrete forming due to its strength and stability. It is commonly used as a beam or joist for formwork systems, providing support for the weight of the concrete. LVL beams and joists can withstand heavy loads, ensuring that the concrete does not collapse or deform during the pouring process. Moreover, LVL beams and joists are easy to cut and shape, allowing for the creation of custom formwork systems.
In summary, Formwork LVL is a versatile and reliable material used extensively in construction for scaffolding and concrete forming. Its strength, stability, and load-bearing capacity make it an invaluable asset in the construction toolbox.
When handling LVL formwork, it is essential to follow strict safety procedures to prevent accidents. Before starting the installation process, ensure that all workers are aware of the safety rules and regulations. Some important safety measures include:
When installing LVL formwork, it is essential to follow proper assembly techniques to ensure that the structure is stable and secure. Some important assembly techniques include:
In conclusion, by following proper safety procedures and assembly techniques, you can ensure that your LVL formwork is installed safely and securely.
Formwork LVL is a durable and long-lasting material that can withstand the wear and tear of construction projects. However, proper maintenance is necessary to ensure its longevity and maximize its lifespan.
Formwork LVL is engineered to withstand heavy loads and harsh conditions, making it an ideal material for construction projects. With proper care and maintenance, it can last for many years, reducing the need for frequent replacements and saving money in the long run.
To ensure the durability of your formwork LVL, it is essential to keep it clean and free from debris. Regular cleaning can help prevent damage and extend its lifespan. It is also important to inspect the formwork regularly for any signs of wear and tear, such as cracks or warping. If any damage is detected, it should be repaired immediately to prevent further damage.
Formwork LVL can be reused multiple times, making it an environmentally friendly choice for construction projects. After use, it can be recycled or repurposed, reducing waste and minimizing the environmental impact of construction projects.
To ensure the formwork LVL can be reused, it is essential to handle and store it correctly. Proper storage can help prevent damage and extend its lifespan. When the formwork is no longer needed, it should be carefully disassembled and stored for future use or recycled.
In summary, proper maintenance is essential to ensure the durability and longevity of formwork LVL. Regular cleaning and inspections can help prevent damage, while proper handling and storage can ensure it can be reused or recycled. By following these guidelines, you can maximize the lifespan of your formwork LVL and reduce the environmental impact of construction projects.
If you are interested in any of our products or would like to discuss a customized order, Please feel free to contact us.