Leading Film Faced Plywood Manufacturing
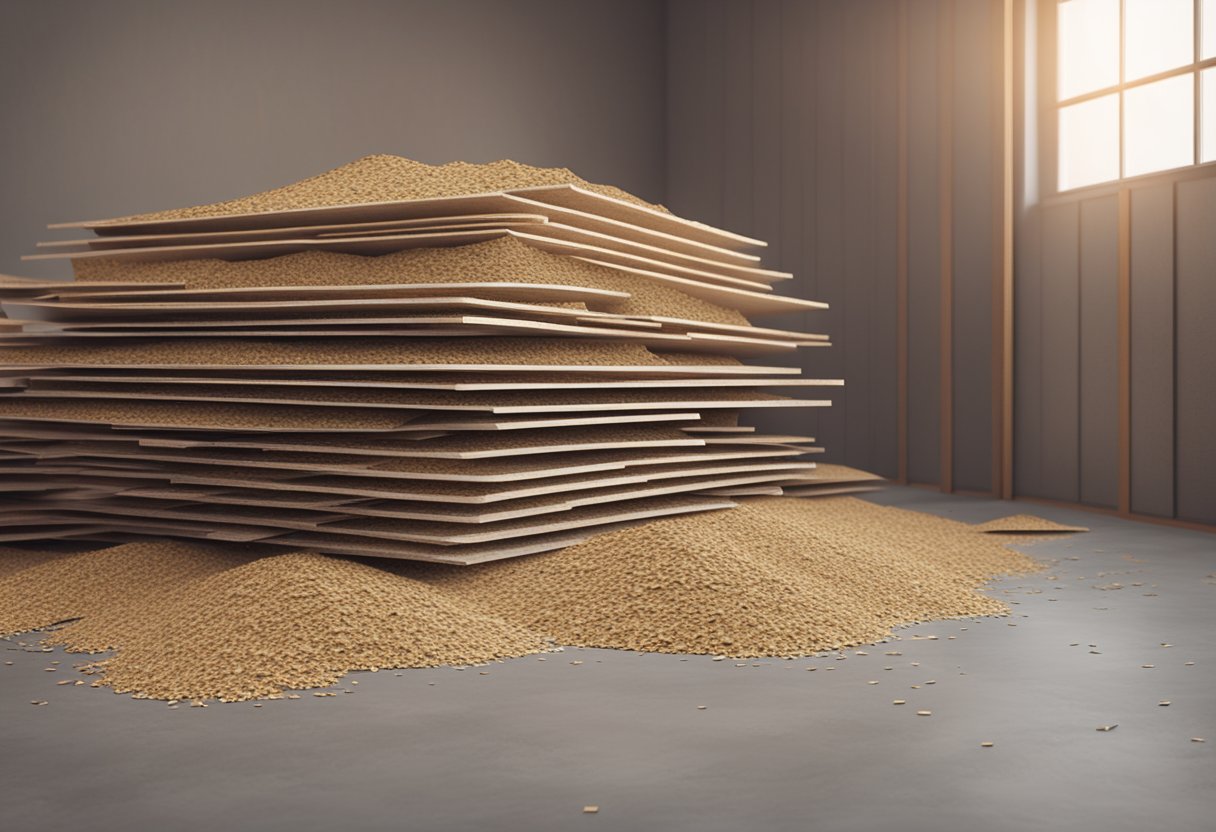
Leading Film Faced Plywood Manufacturing
Coated plywoods is a type of engineered wood product that is made by gluing together thin layers of wood veneer. The surface of the plywood is then coated with a layer of material that provides additional protection and enhances its properties. Coated plywood is known for its durability, strength, and resistance to moisture, making it an ideal choice for a wide range of applications.
There are different types of coated plywood available in the market, each with its unique properties and advantages. Some of the common types of coated plywood include phenolic film-faced plywood, melamine-coated plywood, and vinyl-coated plywood. The manufacturing process of coated plywood involves several steps, including selecting the right type of wood veneer, gluing the veneers together, and applying the coating material.
Coated plywood is widely used in the construction industry for various applications, including flooring, roofing, wall paneling, and furniture making. It is also used in the transportation and marine industries due to its resistance to moisture and weathering. In this article, we will discuss the different types of coated plywood, their manufacturing process, properties, and advantages, common applications, and tips for selecting and purchasing coated plywood.
When it comes to coated plywood, there are several different types to choose from, each with its own unique characteristics and benefits. Here are three of the most common types of coated plywood:
Phenolic film faced plywood is a type of plywood that has a phenolic film coating on both sides. This type of coating makes it highly resistant to moisture, abrasion, and chemicals, making it ideal for use in harsh environments. It is commonly used in construction, transportation, and industrial applications.
Polyurethane coated plywood is a type of plywood that has a polyurethane coating on both sides. This type of coating provides excellent resistance to abrasion and chemicals, making it ideal for use in high-traffic areas. It is commonly used in furniture, cabinetry, and flooring applications.
Melamine coated plywood is a type of plywood that has a melamine coating on both sides. This type of coating provides excellent resistance to scratches, stains, and moisture, making it ideal for use in kitchens, bathrooms, and other high-moisture areas. It is also commonly used in furniture and cabinetry applications.
Overall, coated plywood is a versatile and durable building material that can be used in a wide range of applications. Whether you need a material that is highly resistant to moisture, abrasion, or chemicals, there is a type of coated plywood that is right for your needs.
Coated plywood is made by applying a layer of coating material to the surface of the plywood. The manufacturing process for coated plywood involves several steps that are crucial for ensuring the quality and durability of the final product.
The first step in the manufacturing process is the application of adhesive to the surface of the plywood. The adhesive is applied using a roller or a sprayer, depending on the type of adhesive and the size of the plywood sheets. The adhesive used for coated plywood is typically a resin-based adhesive, such as phenol-formaldehyde or melamine-urea-formaldehyde.
After the adhesive is applied, the plywood sheets are stacked on top of each other and pressed together under high pressure and temperature. This process, known as hot-pressing, ensures that the adhesive bonds the layers of plywood together to create a strong and durable product. The duration of the pressing process varies depending on the thickness and grade of the plywood. The type of adhesive used also plays a key role in the duration of the process.
Once the pressing process is complete, the plywood is cured at a high temperature to ensure that the adhesive is fully cured. This process is critical for ensuring that the adhesive bonds the layers of plywood together effectively.
Another crucial step in the manufacturing process is trimming and finishing. This is because pressing causes the plywood to be oversized and uneven. Trimming ensures that the plywood sheets are the correct size and shape, while finishing ensures that the surface of the plywood is smooth and free of defects.
In conclusion, the manufacturing process for coated plywood involves several crucial steps that are necessary for ensuring the quality and durability of the final product. By carefully selecting high-quality raw materials, applying adhesive, pressing and curing, and trimming and finishing, manufacturers can produce coated plywood that meets the highest standards of quality and performance.
When it comes to construction materials, plywood is a popular choice for many builders and DIY enthusiasts. Coated plywood, in particular, has several properties and advantages that make it an excellent option for various applications.
Coated plywood is known for its durability, which makes it a popular choice for outdoor construction projects. The coating adds an extra layer of protection to the wood, making it resistant to wear and tear caused by exposure to the elements. This durability also makes it an ideal choice for use in high-traffic areas or areas that are prone to damage.
One of the most significant advantages of coated plywood is its water resistance. The coating helps to prevent water from penetrating the wood, which can cause warping, rotting, and other damage. This makes it an ideal choice for use in areas that are exposed to moisture, such as bathrooms, kitchens, and outdoor decks.
Another advantage of coated plywood is its ease of maintenance. The coating helps to protect the wood from stains, scratches, and other damage, making it easy to clean and maintain. This makes it an ideal choice for use in areas that are prone to spills and stains, such as kitchens and dining rooms.
In summary, coated plywood is a durable, water-resistant, and easy-to-maintain material that is ideal for various construction projects. Whether you are building an outdoor deck, renovating your bathroom, or constructing a new kitchen, coated plywood is an excellent choice that will provide you with a long-lasting and reliable solution.
Coated plywood has a wide range of applications across various industries. Its versatility and durability make it a popular choice for numerous projects. Here are some of the most common applications for coated plywood.
Coated plywood is extensively used in the construction industry for framing, sheathing, roofing, and flooring due to its strength and resilience. Its ability to withstand heavy loads and resistance to moisture (when specifically treated) makes it ideal for both interior and exterior structural applications. Coated plywood is also used for concrete formwork due to its smooth surface and ability to resist moisture and chemicals.
Coated plywood is used in furniture making due to its affordability and flexibility. It can be easily cut, drilled, and shaped, allowing for flexible design options. It is commonly used in the manufacturing of cabinets, shelves, desks, and other furniture pieces. Melamine-coated plywood is used in the production of furniture as it provides a smooth and durable surface that is resistant to scratches, stains, and moisture.
Coated plywood is also used in the transportation sector for the construction of floors, walls, and ceilings in vehicles such as buses, trains, and boats. Its lightweight and durable nature make it an excellent choice for this application. Coated plywood is also used in the manufacturing of shipping containers due to its strength and ability to withstand harsh weather conditions.
In summary, coated plywood has a wide range of applications in various industries. Its strength, durability, and affordability make it a popular choice for construction, furniture making, and transportation.
When selecting and purchasing coated plywood, there are a few important factors to consider to ensure you get the best quality product for your project. Here are some tips to help you make an informed decision.
The first thing to consider when selecting coated plywood is the quality standards. Look for plywood that meets the industry standards for quality, such as those set by the American Plywood Association (APA). This will ensure that the plywood is made from high-quality materials and meets the necessary strength and durability requirements for your project.
Another important factor to consider when selecting coated plywood is the thickness and size variations. Plywood comes in various thicknesses, ranging from 1/8 inch to 1 1/4 inch. Make sure to choose the right thickness for your project to ensure that it can support the weight and stress that will be placed on it.
In addition, plywood comes in various sizes, including 4×8 feet, 4×10 feet, and 5×10 feet. Choose the right size for your project to minimize waste and ensure that you have enough plywood to complete the project.
Finally, it is important to consider the reputation of the supplier when purchasing coated plywood. Look for suppliers with a good reputation for quality and customer service. Check customer reviews and ratings to ensure that the supplier has a history of providing high-quality products and excellent customer service.
By considering these factors when selecting and purchasing coated plywood, you can ensure that you get a high-quality product that meets your project’s needs and requirements.
1. What is coated plywood? Coated plywood is a type of engineered wood product made by gluing together thin layers of wood veneer and then applying a protective coating to enhance its properties.
2. What are the common types of coated plywood? Common types of coated plywood include phenolic film-faced plywood, polyurethane-coated plywood, and melamine-coated plywood.
3. What are the advantages of coated plywood? Coated plywood is known for its durability, strength, resistance to moisture, abrasion, and chemicals, making it suitable for various applications. It’s also easy to maintain.
4. What are the main applications of coated plywood? Coated plywood is widely used in the construction industry for flooring, roofing, wall paneling, and concrete formwork. It’s also used in furniture making and in the transportation and marine industries.
5. How is coated plywood manufactured? The manufacturing process involves applying adhesive to the plywood surface, hot-pressing the veneers together, curing the adhesive, and then trimming and finishing the plywood sheets.
If you are interested in any of our products or would like to discuss a customized order, Please feel free to contact us.