Leading Film Faced Plywood Manufacturing
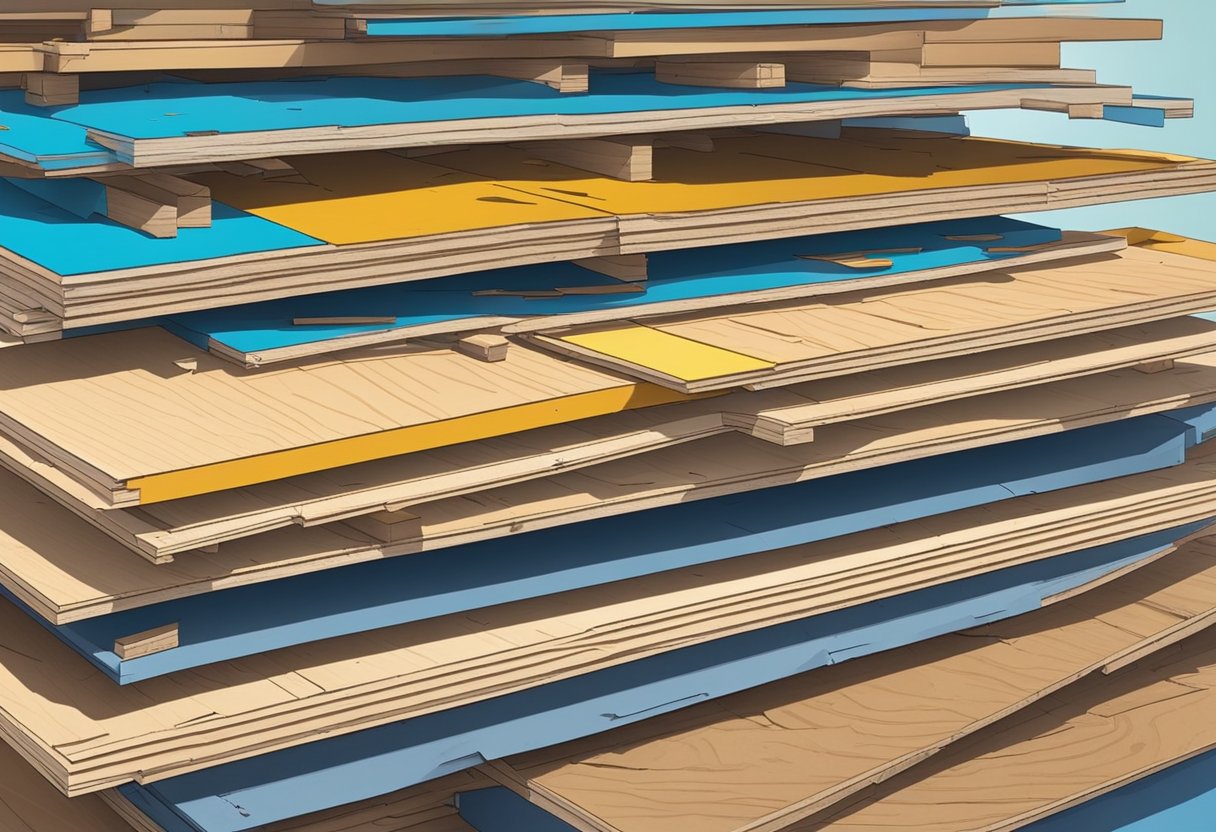
Leading Film Faced Plywood Manufacturing
If you’re planning a construction project, you’ll likely need to use plywood. Plywood is a versatile material that can be used for a range of applications, from building walls and roofs to making furniture. It’s made by gluing together thin layers of wood veneer, with the grain of each layer running in a perpendicular direction to the one below it. This cross-grain construction gives plywood its strength and stability, making it an excellent choice for construction projects.
When it comes to choosing plywood for your project, you’ll need to consider its grade, thickness, and type. Plywood is available in a range of grades, from A to D, with A being the highest quality. The grade refers to the appearance and quality of the surface veneer, with A being smooth and free of knots and defects. The thickness of plywood can vary from 1/8 inch to 1 1/4 inch or more, depending on the application. Finally, the type of plywood you choose will depend on the project’s requirements, whether you need it to be water-resistant, fire-resistant, or simply decorative.
Overall, plywood is an excellent choice for construction projects due to its strength, versatility, and affordability. Understanding the different types of plywood available and their uses will help you choose the right material for your project, ensuring a successful outcome.
When it comes to construction plywood, there are three main types to consider: softwood, hardwood, and tropical plywood. Each type has its own unique characteristics that make it suitable for different types of projects.
Softwood plywood is made from coniferous trees, such as pine or fir. It is the most commonly used type of construction plywood and is often used for structural applications, such as roof decking, walls, and flooring. Softwood plywood is typically less expensive than hardwood plywood, making it a popular choice for budget-conscious builders.
Hardwood plywood is made from deciduous trees, such as oak or maple. It is known for its strength, durability, and attractive appearance. Hardwood plywood is often used for furniture, cabinetry, and decorative paneling. It is more expensive than softwood plywood, but its superior quality makes it worth the investment.
Tropical plywood is made from tropical hardwoods, such as meranti or okoume. It is known for its resistance to moisture and decay, making it ideal for outdoor applications such as boat building and exterior construction. Tropical plywood is also used for decorative paneling and furniture. It is more expensive than softwood plywood but less expensive than hardwood plywood.
When choosing construction plywood, consider the specific needs of your project. Softwood plywood is a good choice for structural applications, while hardwood plywood is best for decorative and high-quality projects. Tropical plywood is ideal for outdoor applications where moisture resistance is important.
If you are interested in learning about the manufacturing process of construction plywood, you’re in the right place. In this section, we will discuss the three main steps involved in the plywood manufacturing process: Veneer Peeling, Gluing and Pressing, and Finishing and Trimming.
The first step in the manufacturing process of construction plywood is veneer peeling. This process involves peeling thin sheets of wood from a log using a rotary lathe. The thickness of the veneer depends on the intended use of the plywood. The veneers are then sorted by size and quality.
Once the veneers have been peeled and sorted, they are glued together in layers with their grains perpendicular to one another. This cross-grain construction gives plywood its strength and durability. The type of adhesive used plays a key role in the durability of the plywood. The glued veneers are then pressed together under high pressure and high temperature to form a flat and uniform panel.
The final step in the manufacturing process of construction plywood is finishing and trimming. The pressed plywood panels are trimmed to size and sanded to a smooth finish. The sanding process removes any rough edges and ensures that the plywood has a uniform thickness. The plywood sheets are then stacked and wrapped in protective materials to prevent damage during transportation.
In summary, the manufacturing process of construction plywood involves veneer peeling, gluing and pressing, and finishing and trimming. Each step is crucial in ensuring that the plywood is strong, durable, and of high quality.
When it comes to construction plywood, there are several important properties and specifications to consider. In this section, we’ll take a closer look at thickness and sizes, grading and standards, and moisture content and durability.
Construction plywood comes in a variety of thicknesses and sizes to meet the needs of different projects. Standard thicknesses range from 1/8 inch to 1 1/4 inch, with 1/4 inch, 1/2 inch, and 3/4 inch being the most common. The size of the plywood sheets also varies, with standard sheets measuring 4 feet by 8 feet. However, larger sheets are available for some applications.
Plywood is graded based on its appearance and quality, with different grades suitable for different applications. The most common grading system used in the United States is the Voluntary Product Standard PS 1-09, which sets standards for both structural and non-structural plywood. The grading system takes into account factors such as the number and size of knots, the presence of voids or splits, and the overall appearance of the plywood.
Moisture content is an important consideration when it comes to construction plywood. Plywood with a high moisture content is more susceptible to warping, while plywood with a low moisture content is more stable. In addition, the durability of the plywood is affected by the type of glue used to bond the layers together. Exterior-grade plywood is designed to withstand exposure to the elements, while interior-grade plywood is not.
Overall, the properties and specifications of construction plywood are important factors to consider when selecting the right plywood for your project. By understanding the different thicknesses and sizes, grading and standards, and moisture content and durability, you can make an informed decision and ensure that your project is successful.
Plywood is a versatile material that is widely used in various construction applications. It offers both structural and non-structural capabilities, making it an essential element in building projects of all sizes. In this section, we will discuss some of the most common applications of plywood in construction.
Plywood is commonly used in construction for its strength and durability. It is often used as a substitute for traditional lumber because it is more stable and less prone to warping. Plywood is also used for sheathing and subflooring because of its ability to distribute loads evenly. It is also used in roofing and wall systems because of its resistance to bending and cracking.
Plywood is an excellent material for flooring and walls because it is easy to install and provides a smooth surface for finishing. It is often used as a base for hardwood flooring, carpeting, and tile. Plywood is also used for wall sheathing because it provides a stable surface for attaching siding or other exterior finishes.
Plywood is commonly used as formwork and shuttering for concrete structures. It is an ideal material for this application because it is strong, durable, and easy to work with. Plywood is also used for concrete form liners, which create decorative patterns and textures on the surface of concrete structures.
Plywood is a versatile material that is widely used in construction for its strength, durability, and ease of use. Whether you are building a new home or renovating an existing one, plywood is an excellent choice for a variety of applications.
When working with construction plywood, it is important to prioritize safety. Here are some tips to ensure that you handle plywood safely:
When moving plywood sheets, it is important to use proper lifting techniques. Bend your knees, keep your back straight, and use your legs to lift the load. This reduces the risk of back strain and damage to the plywood. Use a rolling cart to move plywood sheets, or if you need to lift them, use a 12-foot-long rope to move sheets by tying loops on each end of the rope and then place the loops around the bottom corners of a sheet; then, pull up on the center of the rope for a “handle” and lift up (it will still be heavy, but a bit less awkward to move) If project components do not allow for a rolling cart, then use a dolly.
When storing plywood, it is important to keep it dry and flat. Plywood should be stored in a covered area to prevent exposure to moisture, which can cause warping or delamination. You should also stack plywood sheets flat on a level surface, supported by evenly spaced stickers or spacers. This will help prevent damage to the edges and surface of the plywood.
When cutting plywood, always use a sharp blade. Dull blades can cause the plywood to splinter or tear, which can be dangerous. Also, when working with power tools, always wear eye and ear protection.
When installing plywood, it is important to follow the manufacturer’s instructions. Use the appropriate fasteners and spacing, and make sure that the plywood is properly supported. If you are unsure about how to install plywood, consult a professional.
When working with plywood, it is important to wear personal protective equipment (PPE). This includes eye protection, ear protection, and a dust mask. Plywood can create a lot of dust, which can be harmful if inhaled. A dust mask will help prevent respiratory problems. Eye and ear protection will protect you from flying debris and loud noises.
By following these safety tips, you can ensure that you handle plywood safely and avoid accidents.
1. What is plywood and why is it used in construction projects?
Plywood is a versatile construction material made by gluing together thin layers of wood veneer. Its cross-grain construction provides strength and stability, making it suitable for various applications like building walls, roofs, and furniture.
2. What factors should I consider when choosing plywood for my project?
When selecting plywood, consider its grade, thickness, and type. Grades range from A to D, with A being the highest quality. Thickness varies depending on the application. Types include softwood, hardwood, and tropical plywood, each with unique characteristics.
3. Can you explain the different types of construction plywood available?
Certainly! There are three main types: softwood plywood, made from coniferous trees like pine; hardwood plywood, crafted from deciduous trees like oak; and tropical plywood, derived from tropical hardwoods such as meranti. Each type has distinct properties suitable for different projects.
4. What is the manufacturing process of construction plywood?
The manufacturing process involves veneer peeling, where thin wood sheets are extracted from logs; gluing and pressing, where these veneers are bonded together with adhesive under pressure; and finishing and trimming, where the panels are cut to size and sanded for a smooth finish.
5. What are some important properties and specifications of construction plywood?
Key considerations include thickness and sizes, grading and standards, and moisture content and durability. Plywood thickness typically ranges from 1/8 inch to 1 1/4 inch, with common sizes like 4 feet by 8 feet. Grading systems assess appearance and quality, while moisture content affects stability and durability.
If you are interested in any of our products or would like to discuss a customized order, Please feel free to contact us.